Lò nung cảm ứng là gì?
Lò nung cảm ứng là lò điện sử dụng cảm ứng điện từ để làm nóng và làm tan chảy kim loại. Nó thường được sử dụng trong ngành công nghiệp đúc để bôi và tinh chỉnh các kim loại như sắt, Thép, đồng, nhôm, và các hợp kim khác.
Nguyên tắc làm việc cơ bản của lò nung cảm ứng.
Nguyên tắc cơ bản đằng sau các lò cảm ứng liên quan đến việc sử dụng dòng điện xen kẽ (AC) thông qua một cuộn dây đồng, tạo ra từ trường. Khi một vật kim loại, chẳng hạn như một vật liệu rương hoặc tích điện, được đặt bên trong một cuộn dây, một từ trường tạo ra một dòng điện trong kim loại, được gọi là dòng điện Eddy. Do điện trở của kim loại, Các dòng xoáy này tạo ra nhiệt, khiến nó nóng lên và tan chảy nhanh chóng.
Thành phần của lò nung cảm ứng
Thành phần của lò nung cảm ứng đề cập đến các thành phần và vật liệu khác nhau tạo nên cấu trúc của lò và làm cho nó hoạt động. Trong khi thành phần chính xác có thể thay đổi theo thiết kế và nhà sản xuất, Sau đây là các thành phần phổ biến được tìm thấy trong lò nung cảm ứng:
nồi nấu kim loại:
Một cái nồi nấu kim loại là một thùng chứa điện tích kim loại trong quá trình nóng chảy. Nó thường được làm bằng vật liệu chịu lửa và có thể chịu được nhiệt độ cao và phản ứng hóa học với kim loại nóng chảy.
cuộn dây cảm ứng:
Một cuộn dây cảm ứng là một dây dẫn đồng được đặt xung quanh hoặc gần với một cái nồi nấu kim loại. Nó chịu trách nhiệm tạo ra một từ trường xen kẽ, tạo ra dòng điện xoáy trong điện tích điện kim loại, khiến nó nóng lên và tan chảy.
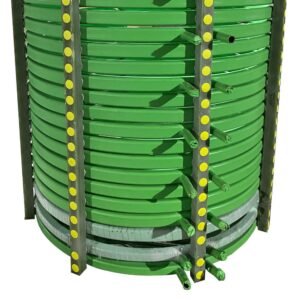
Cung cấp điện:
Nguồn điện cung cấp năng lượng điện cần thiết cho hoạt động của lò nung cảm ứng. Nó thường bao gồm một mức cao, Nguồn cung cấp năng lượng giữa tần số chuyển đổi công suất đầu vào thành tần số và điện áp mong muốn phù hợp để sưởi ấm cảm ứng.
Hệ thống làm mát:
Lò nung cảm ứng tạo ra nhiều nhiệt trong quá trình hoạt động và yêu cầu một hệ thống làm mát để ngăn chặn quá nhiệt. Hệ thống thường bao gồm các thành phần làm mát bằng nước như cuộn cảm ứng, Cáp điện, và các thành phần quan trọng khác để duy trì nhiệt độ hoạt động tối ưu.
Hệ thống điều khiển:
Lò cảm ứng được trang bị hệ thống điều khiển cho phép người vận hành giám sát và điều chỉnh các tham số khác nhau như đầu vào công suất, nhiệt độ, và chu kỳ nóng chảy. Nó có thể bao gồm các cảm biến nhiệt độ, bộ điều khiển điện, hẹn giờ, và các tính năng an toàn để đảm bảo hoạt động hiệu quả và an toàn.
Hệ thống cho ăn:
Lò nung cảm ứng lớn hơn thường có một hệ thống sạc để tạo điều kiện cho việc đưa điện tích kim loại vào nồi nấu kim loại. Điều này có thể bao gồm các cơ chế như hệ thống thủy lực, Sạc plungers hoặc băng tải để vận chuyển nguyên liệu thô vào lò.
Lớp lót chịu lửa:
Lớp lót của nồi nấu kim loại và các phần liên quan khác của lò thường được lót bằng vật liệu chịu lửa để cung cấp vật liệu cách nhiệt và bảo vệ cấu trúc khỏi nhiệt độ cao và tác dụng ăn mòn của kim loại nóng chảy.
Hệ thống ống xả:
Tùy thuộc vào ứng dụng, Lò nung cảm ứng có thể bao gồm một hệ thống ống xả để loại bỏ bất kỳ khói nào, khí, hoặc các sản phẩm phụ được tạo ra trong quá trình tan chảy. Điều này giúp duy trì môi trường làm việc an toàn và thúc đẩy chất lượng không khí.
Loại lò nung cảm ứng
Đây là những thành phần và vật liệu chính trong lò nung cảm ứng. Thiết kế cụ thể, kích thước, và các tính năng bổ sung có thể khác nhau tùy thuộc vào mục đích sử dụng và thông số kỹ thuật của nhà sản xuất.
Có nhiều loại lò nung cảm ứng, có thể được chia thành các loại sau theo các ứng dụng và yêu cầu thiết kế khác nhau:
Lò nhận cảm ứng tần số công nghiệp:
Loại lò này áp dụng nguồn cung cấp năng lượng tần số công nghiệp (Máy biến áp đặc biệt) để nấu chảy.
Lò nung cảm ứng tần số trung bình:
Lò cảm ứng tần số trung bình là một tên phổ biến cho lò cảm ứng không VACUUM. Nó sử dụng biến tần thyristor hoặc hệ số nhân tần như nguồn điện để tăng tần số từ 50Hz (60Hz) đến 150 ~ 4000Hz. Nó là một nhánh quan trọng của lò nung cảm ứng, Chủ yếu được sử dụng để luyện thép đặc biệt, với công suất lò là 0,10 ~ 60t.
Lò cảm ứng chân không:
Loại lò này được nấu chảy và đổ vào chân không. Nguồn điện tương tự như nguồn điện của lò cảm ứng tần số trung bình. Nó chủ yếu được sử dụng để bôi thép và hợp kim đặc biệt. Công suất lò 0,05 ~ 60T.
Lò cảm ứng plasma:
Loại lò này được nấu chảy trong khí bảo vệ và được làm nóng bởi nguồn cung cấp năng lượng plasma và nguồn cung cấp năng lượng lò nung tần số trung bình. Nó chủ yếu được sử dụng trong sản xuất carbon cực thấp, Thép đặc biệt lưu huỳnh và phốt pho và hợp kim. Dung tích lò là 0,5 ~ 2t.
Lò cảm ứng điều áp:
Loại lò này áp dụng hệ thống cảm ứng tần số trung bình dưới áp suất nitơ là 0,2 ~ 2,0MPa trong nồi nấu kim loại để tan chảy và đúc thép nitơ cao có chứa N≥0,60%. Công suất lò là 0,05 ~ 10T.
Quá trình gia nhiệt cảm ứng của lò nung cảm ứng
Quá trình gia nhiệt cảm ứng của lò cảm ứng chủ yếu tạo ra một từ trường xen kẽ trong cuộn dây thông qua dòng điện xen kẽ, và khi phần kim loại được đặt trong cuộn dây, Phần kim loại tạo ra dòng xoáy tuần hoàn. Những dòng điện này chống lại điện trở của kim loại, tạo ra nhiệt địa phương chính xác mà không cần tiếp xúc trực tiếp giữa bộ phận và cuộn dây. Phương pháp sưởi ấm này có thể chuyển đổi hiệu quả năng lượng điện thành năng lượng nhiệt, và nhiệt độ và vùng sưởi ấm có thể được kiểm soát chính xác, giúp tránh quá nóng hoặc thiệt hại của vật liệu.
Các yếu tố ảnh hưởng đến hiệu quả của việc sưởi ấm cảm ứng chủ yếu là tần số, Thiết kế năng lượng và cuộn dây.
Tính thường xuyên:
Tần suất sưởi ấm cảm ứng thường là tần số của dòng điện xen kẽ, Nói chung từ 50Hz đến 50kHz. Tần số cao hơn có thể tạo ra nhiều dòng điện xoáy hơn, Đang nóng lên nhanh hơn. Tuy nhiên, Sự lựa chọn tần số cũng bị giới hạn bởi vật liệu và kích thước của kim loại, bởi vì tín hiệu tần số cao có thể làm tăng trở kháng điện bên trong kim loại, dẫn đến giảm hiệu quả sưởi ấm. Vì thế, cần phải chọn tần số thích hợp theo tình huống cụ thể trong ứng dụng thực tế.
Quyền lực:
Sức mạnh đề cập đến năng lượng được cung cấp trên mỗi đơn vị thời gian. Trong hệ thống sưởi ấm, Nhiều năng lượng hơn thường có nghĩa là sưởi ấm nhanh hơn. Tuy nhiên, Quá nhiều năng lượng có thể khiến kim loại quá nóng, làm hỏng vật liệu. Vì thế, cần phải chọn đúng năng lượng theo nhu cầu thực tế.
Thiết kế cuộn dây:
cuộn dây là một trong những thành phần chính trong hệ thống sưởi cảm ứng, và thiết kế của nó có tác động quan trọng đến hiệu quả sưởi ấm. Ví dụ, hình dạng, kích cỡ, và vị trí của cuộn dây đều ảnh hưởng đến phân phối từ trường và sự hình thành của dòng điện xoáy. Thiết kế cuộn dây hợp lý có thể tối ưu hóa phân phối từ trường và cải thiện hiệu quả sưởi ấm. Ngoài ra, Sự lựa chọn vật liệu cuộn dây cũng rất quan trọng, bởi vì các vật liệu khác nhau có độ dẫn điện và điện trở khác nhau, điều này sẽ ảnh hưởng đến tuổi thọ dịch vụ và hiệu quả sưởi ấm của cuộn dây.
Tóm lại, Tính thường xuyên, quyền lực, và thiết kế cuộn dây là những yếu tố chính ảnh hưởng đến hiệu quả của việc sưởi ấm cảm ứng. Trong các ứng dụng thực tế, Cần phải chọn và tối ưu hóa theo tình huống cụ thể để cải thiện hiệu quả sưởi ấm và tránh thiệt hại vật liệu.