Induction furnace control systems play a vital role in modern industrial production. They are widely used and powerful.
Just like the human nervous system, the induction furnace control system is like the “Trung tâm thần kinh” của lò nung cảm ứng, sensing the state of the furnace in real time, accurately controlling the heating process, and ensuring the stability of the production process and the excellence of product quality.
Main application areas
Lò nung cảm ứng, đó là, induction heating electric furnaces with operating frequencies ranging from hundreds of hertz to tens of kilohertz, are widely used in many industrial fields due to their high efficiency, Tiết kiệm năng lượng, và bảo vệ môi trường. Advanced control systems are the key to ensuring their stable operation and optimizing production processes.
Smelting and heating
Metal smelting and heating are undoubtedly the core application areas of induction furnaces. Whether it is the perfection of steel smelting or the excellence of non-ferrous metal smelting, the induction furnace control system can provide high-quality molten metal for the foundry industry with its precise power regulation and temperature control. From cast iron parts to complex alloy components, the control system can ensure that the metal is melted, kept warm, and even overheated at the optimal temperature, laying a solid foundation for subsequent casting molding. It can be said that the induction furnace control system is the “golden finger” for the foundry industry to create fine products.
Heat treatment and forging
The performance of metals depends largely on their heat treatment process. When the induction furnace is used in heat treatment links such as quenching, ủ, and annealing, the control system can accurately control the heating temperature and heating rate to ensure that the metal material completes the organizational transformation under the best conditions, thereby obtaining the required hardness, strength and toughness. Similarly, in the forging heating link, uniform temperature distribution is the key to ensuring the quality of forgings, and this is also inseparable from the precise control of the control system.
Powder metallurgy and crystal growth
In the field of powder metallurgy, the induction furnace control system can accurately control the sintering temperature and heating curve to help the powder pressed blank achieve full sintering and improve the density and mechanical properties of the product. In the single crystal growth process of semiconductor materials, the precise control of the temperature gradient is even more important.
Pipeline heating and special applications
The induction furnace control system also plays an important role in pipeline heating, welding preheating, và các lĩnh vực khác. In the petroleum, chemical and other industries, it can provide local or overall precise heating for the pipeline to improve welding quality and efficiency. Even in some scientific research fields, induction furnaces have become a powerful assistant for high-temperature experiments and material research.
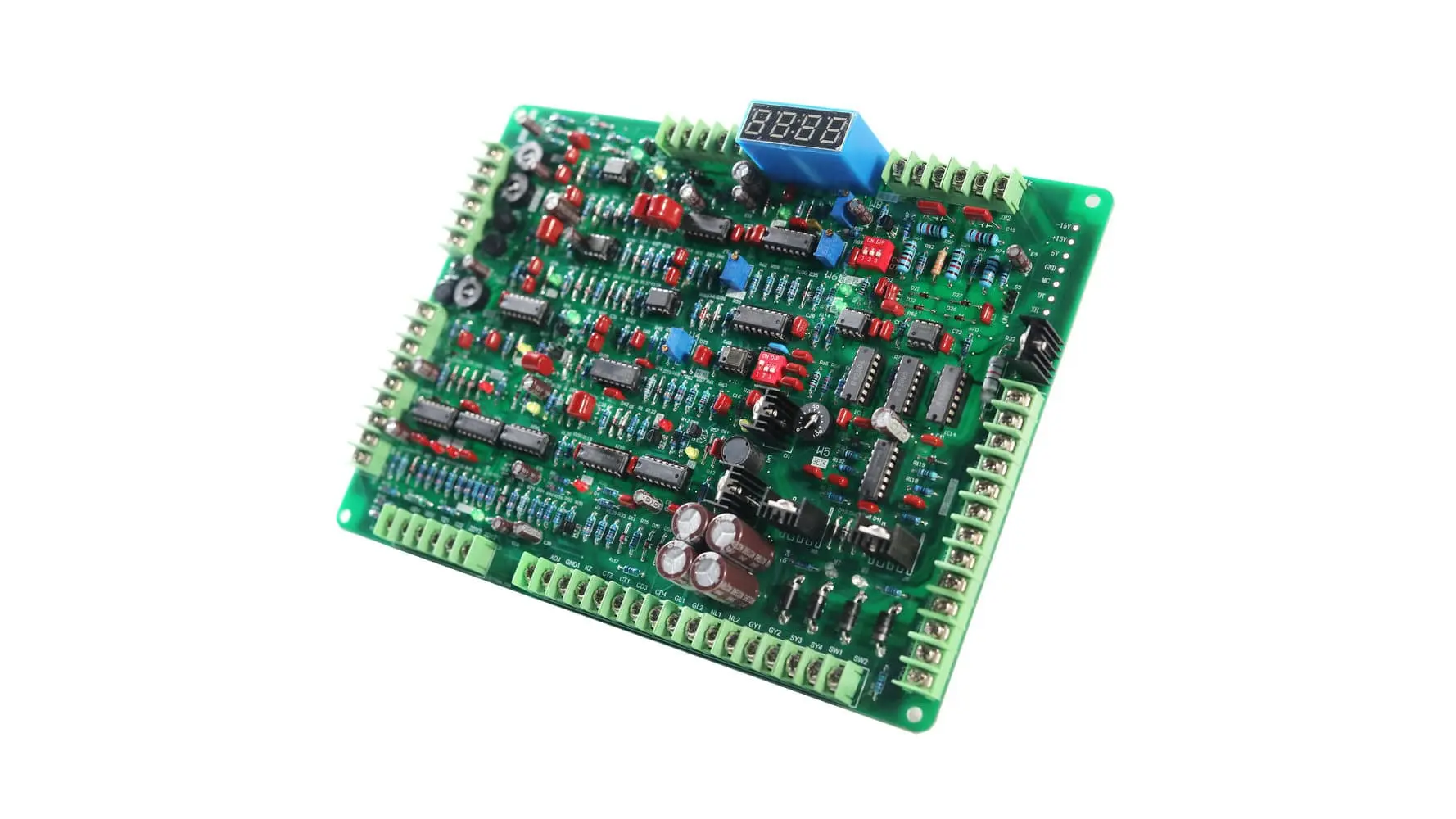
Functional manifestation of the control system
In the above application, the induction furnace control system mainly realizes the following functions to ensure the stability of the production process and product quality:
- Power regulation and control: Accurately adjust the output power of the induction power supply according to the process requirements to achieve rapid heating, precise temperature control and stable insulation.
- Kiểm soát nhiệt độ: Real-time monitoring of the temperature in the furnace through the temperature sensor, and closed-loop control according to the set temperature curve to ensure that the heating process meets the process requirements.
- Frequency tracking and adjustment: Automatically track the changes in load impedance and adjust the output frequency of the induction power supply so that the equipment always works in the best resonant state to improve efficiency.
- Fault diagnosis and protection: Real-time monitoring of the system operation status. When overcurrent, quá điện áp, overheating and other faults occur, it can promptly alarm and take protective measures to prevent equipment damage.
- Process parameter setting and storage: Allow users to set parameters such as heating temperature, insulation time, heating rate, vân vân. according to different workpieces and process requirements, and can store multiple process plans for easy call.
- Automatic control: Combine PLC, touch screen, vân vân. to realize automatic control of the heating process, reduce manual intervention, and improve production efficiency and consistency.
- Data collection and monitoring: Record key data such as temperature and power during the heating process to facilitate process analysis and quality traceability.
Summary
The application of induction furnace control systems covers almost all industrial fields that require heating of metals or other materials. With the continuous development of automation and intelligent technology, modern induction furnace control systems are developing towards higher precision, higher efficiency, more intelligence, and easier operation, providing strong support for improving production efficiency and product quality assurance in various industries.
The control system of the future will be more intelligent and networked, and will be able to achieve more advanced functions such as remote monitoring, fault prediction, and process optimization, bringing higher efficiency and better quality to industrial production.
The induction furnace control system is the “smart brain” that works silently in the field of industrial heating. With its precise control and powerful functions, it drives the production progress of various industries.