การหลอมเหล็กเป็นกระบวนการที่ซับซ้อนและซับซ้อนซึ่งเกี่ยวข้องกับกระบวนการและเทคโนโลยีที่หลากหลาย.
Selection of raw materials
1. Types of iron ore:
Iron ore is the main raw material for iron smelting. Common types of iron ore include hematite, magnetite, limonite, ฯลฯ. Their chemical composition and ore structure influence the ore reduction properties during smelting, slag formation and final iron quality. ดังนั้น, it is crucial to select the right iron ore based on the required iron content and quality characteristics.
2. Ore quality:
The quality of ore is directly related to the cost and efficiency of iron smelting. High-quality ores typically contain higher metal content, small amounts of impurities and minerals, which contribute to increased iron production and quality.
3. Sulfur content:
Sulfur is a common ore impurity. Ore with high sulfur content will increase the formation of slag and have a negative impact on the quality of iron. ดังนั้น, attention needs to be paid to controlling the sulfur content when selecting ores to ensure the quality of the final product.
4. Moisture and particle size:
The moisture and particle size of the ore are also important considerations. Appropriate humidity and particle size contribute to the uniform distribution and effective reaction of ore in the blast furnace, จึงปรับปรุงประสิทธิภาพการหลอม.
5. Raw material ratio:
In addition to iron ore, other auxiliary raw materials may also be added, such as coke, limestone, ฯลฯ. The ratio and quality of these raw materials also have an impact on the smelting process and the performance of the final product, and need to be reasonably prepared according to the specific process and iron requirements.
Selection of melting equipment
1. Blast Furnace:
The blast furnace is the equipment most commonly used for large-scale iron smelting. It is usually a huge vertical cylindrical structure used to reduce iron ore and coke into pig iron at high temperatures. Blast furnace operations are complex and require control of temperature, gas flow, and raw material inputs to ensure efficient reduction and melting processes.
2. Electric arc furnace:
Electric arc furnaces use electrical energy to generate high temperatures to melt scrap steel or ferroalloys into liquid metal. It is often used to recycle and reuse scrap metal and is an environmentally friendly furnace type. The advantages of electric arc furnaces are that the temperature is easy to control and they are suitable for the production of special alloys.
3. เตาเหนี่ยวนำ:
An induction furnace is also a device that uses electromagnetic induction to heat metal. It can be used to melt metal. Induction furnaces are usually used in small-scale production and are more suitable for the production of high-quality and special alloys.
4. Oxygen converter:
Oxygen converter is a steel smelting equipment that oxidizes scrap steel or ferroalloy by injecting oxygen into the converter to achieve smelting and alloying. This type of furnace is used for mass production of different types of steel alloys.
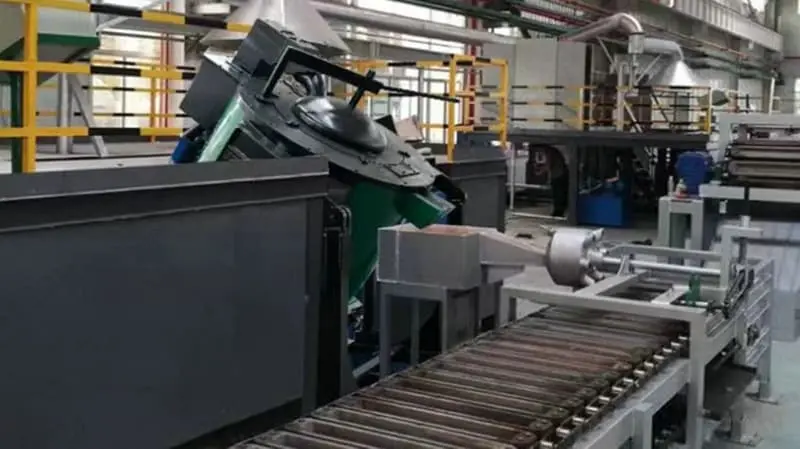
Melting equipment operation
1. การตระเตรียม:
Before starting the smelting process, the furnace needs to be prepared, including cleaning the furnace, inspecting the equipment, and preparing the required raw materials.
2. Raw material input:
Put the pre-mixed proportions of iron ore, coke, scrap steel and other raw materials into the furnace according to the set proportion. This step requires precise control based on process requirements and furnace capacity.
3. Ignition and heating:
Depending on the type of smelting equipment, ignition is performed after the raw materials are put in to start heating the furnace. Heat energy is provided through fuel combustion, electrical energy input, or other means to raise the temperature in the furnace to the temperature required to melt the metal.
4. Furnace reaction control:
Once the furnace temperature reaches the desired level, the reactions in the furnace need to be controlled. In the blast furnace, the reduction reaction is controlled by injecting air or other reducing agents to reduce iron ore into pig iron.
5. Monitoring and adjustment:
During the entire smelting process, parameters such as temperature, ความดัน, and chemical reactions need to be monitored in real time through sensors, monitoring systems and other equipment. Make adjustments based on the monitoring results to keep the reaction in the furnace in a stable state.
6. Slag treatment:
Slag is a non-metallic by-product produced during the smelting process and needs to be cleaned and processed regularly to maintain the furnace environment and product quality.
7. Product collection and processing:
Depending on the characteristics of the smelting equipment, the smelting products, which may be molten metal or slag, are collected for subsequent processing and separation.
Iron melting process
1. Furnace charge preparation:
Iron ore, coke and limestone are mixed according to a certain proportion to prepare the furnace charge. The proportion of charge will affect the chemical reactions and slag properties during the ironmaking process.
2. Blast furnace charging:
Put the pre-prepared charge into the top of the blast furnace layer by layer. The charge is usually added to the blast furnace from the top through a hopper to evenly distribute the charge.
3. Smelting process:
Reduction stage: At high temperatures, the carbon in the coke and the heat generated by combustion cause the iron oxides in the iron ore to be reduced to metallic iron. This process produces some by-products such as carbon dioxide and some oxides.
Slag formation: During the reduction process, limestone acts as a flux and helps in the formation of slag. Slag is mainly composed of impurities and non-metallic substances during the smelting process. It floats on the molten iron and isolates the iron from contact with the air, reducing the oxidation of the iron.
Pig iron collection: Molten metallic iron is collected at the bottom of the blast furnace, this is pig iron. The quality of pig iron depends on the proportion of charge, temperature control and the stability of the reaction in the furnace.
4. Iron tapping and slag discharge:
Iron is regularly tapped from the bottom of the blast furnace, and pig iron is collected and transported to subsequent processing processes. ในเวลาเดียวกัน, the slag will be cleaned regularly to ensure the normal operation of the blast furnace.
5. Furnace post-processing:
After pig iron is obtained, further smelting or alloying may be required to achieve the desired steel product specifications and quality.
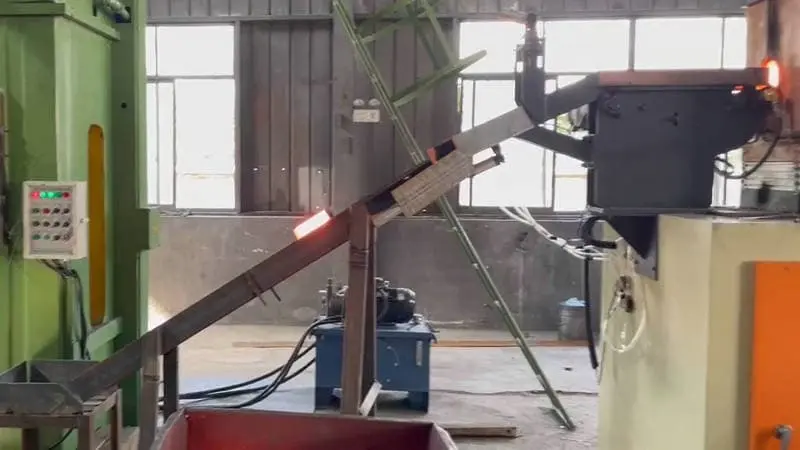
Alloying process
1. การเพิ่มองค์ประกอบโลหะผสม:
During the smelting process, the chemical composition of pig iron can be adjusted by adding alloying elements. Commonly used alloying elements include manganese, โครเมียม, molybdenum, นิกเกิล, vanadium, ฯลฯ. Each element gives steel specific properties, such as increased hardness, ความต้านทานการกัดกร่อน, ความแข็งแกร่ง, และอื่น ๆ.
2. Alloying reaction:
The addition of alloying elements is usually achieved by adding alloyed iron, alloyed ores or other compounds containing required elements to the iron-making process, allowing the alloying elements to react with pig iron, thereby achieving alloying treatment. This process requires precise control of temperature and chemical reaction conditions.
3. The role of alloying:
Different alloying elements will have different effects on steel. ตัวอย่างเช่น, adding chromium can improve the corrosion resistance of steel; manganese can increase strength and hardness; molybdenum can improve the toughness of steel, ฯลฯ. Alloying treatment can adjust the amount and type of alloying elements added according to the required product properties.
4. Temperature control and mixing:
Alloying usually requires reheating and mixing the pig iron to ensure that the alloying elements are fully dissolved and distributed in the steel to obtain a uniform chemical composition.
5. Online alloying:
In modern processes, some alloying elements can be added online, that is, the controlled addition of elements is achieved by spraying alloying materials or other methods during the ironmaking process, thereby more accurately controlling the chemical composition of steel.
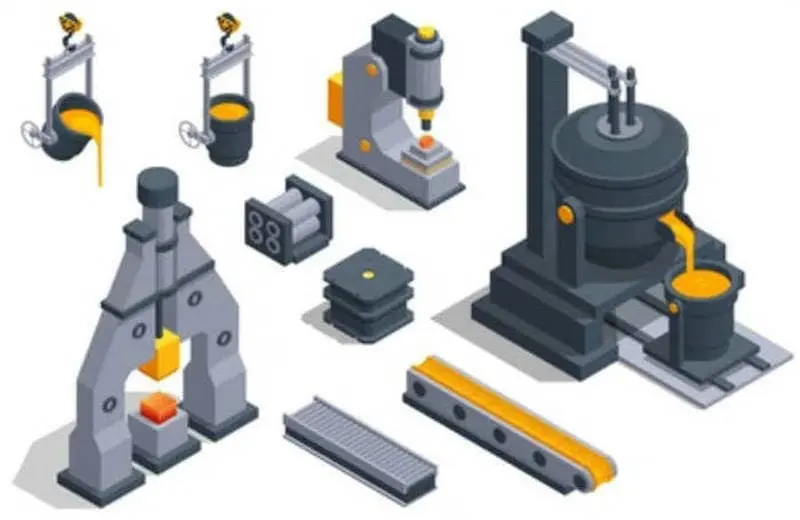
การคุ้มครองสิ่งแวดล้อม
1. Exhaust gas emission control:
The combustion and smelting process in the furnace will produce a large amount of exhaust gas, which may contain harmful substances such as sulfur dioxide, nitrogen oxides, ฯลฯ. The use of in-furnace injection control technology, exhaust gas treatment devices and other technologies can effectively reduce and control exhaust gas emissions.
2. Slag Disposal:
Slag is a by-product of the smelting process and may contain heavy metals and other harmful substances. Adopting appropriate slag treatment technologies, such as recycling and reuse, can help reduce environmental impact.
3. Resource recycling:
Using renewable resources for iron making through scrap steel recycling and other methods can help reduce the demand for original ore, reduce resource consumption and environmental load.
4. Application of environmental protection technology:
The use of advanced environmental protection technology, such as flue gas desulfurization, dust collectors, waste heat recovery, ฯลฯ, can reduce pollutant emissions and improve resource utilization.
ความปลอดภัย
1. Process safety:
The smelting process involves high temperatures and high pressures, and workers need to strictly abide by operating procedures and wear personal protective equipment to ensure process safety.
2. Equipment safety:
The normal operation of iron-making equipment is crucial to worker safety. The status of the equipment needs to be checked regularly to ensure stable and reliable operation of the equipment.
3. Emergency plan:
Establish a complete emergency plan to prevent and deal with possible unexpected situations to ensure personnel safety and equipment integrity.
4. Occupational health:
People who have been engaged in iron-making work for a long time need to pay attention to occupational health issues, conduct regular physical examinations and health monitoring, and avoid the risks of occupational diseases.
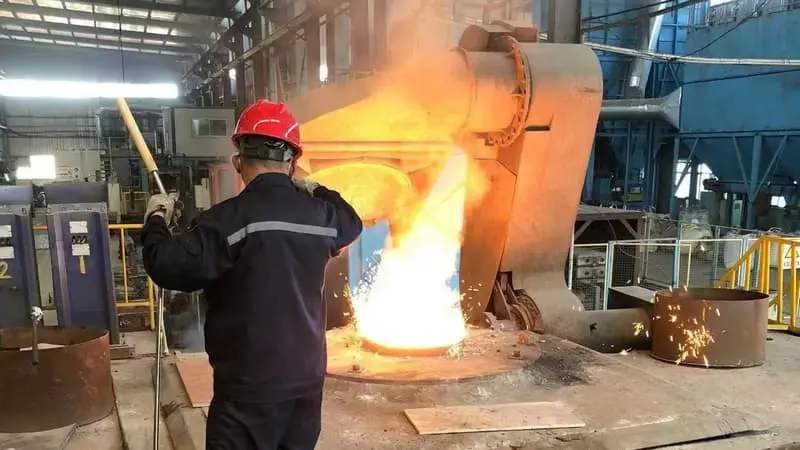
ระบบอัตโนมัติ
1. Intelligent control system:
Modern iron smelting plants often use intelligent control systems to realize automated monitoring and regulation of the smelting process through sensors, monitoring equipment and computer control systems. These systems can collect data in real time, analyze furnace parameters, and automatically adjust according to preset conditions to improve production efficiency and product quality.
2. Remote monitoring and management:
Using information technology, iron smelting plants can achieve remote monitoring and management. This means that production personnel can monitor the operation of the production line through the remote system, respond and handle abnormal situations in a timely manner, and improve the response speed and accuracy of production.
3. Automation devices and robotics:
ในกระบวนการถลุง, automation devices and robotics are widely used, such as automatic feeding systems, robots for cleaning slag, automatic measurement and sampling devices, ฯลฯ. These devices and technologies can improve production efficiency and reduce labor costs. Also adds security.
4. Digitization and data analysis:
Iron smelting companies use digital technology and data analysis to optimize and improve the production process. Through big data analysis, potential problems in production can be discovered, process flows can be optimized, and more effective solutions can be proposed to continuously improve production efficiency and product quality.
5. Energy conservation and emission reduction:
Modern iron smelting plants focus on energy conservation and emission reduction, adopt advanced energy management technology and equipment, and reduce energy consumption and emissions through waste heat recovery, comprehensive utilization of resources and other means to achieve sustainable development.