Induction melting process
The induction melting process is a modern metal processing method that uses the principle of induction heating to melt metal. It is based on the principle of electromagnetic induction, which generates induced current in metal conductors through high-frequency alternating current, thereby causing the metal material to rapidly heat up and reach the melting temperature.
This process involves several key steps:
Induction heating:
Use an induction heating device to generate a high-frequency alternating electromagnetic field near metal materials. This electromagnetic field creates an induced current in the metal conductor, causing the conductor to heat up rapidly.
Melting Metal:
The heat generated by the induced current in a metal conductor causes the metal material to rapidly heat up, reach its melting point and begin to melt. This puts the metal into a liquid state that can be shaped into desired shapes or used for other processing.
การควบคุมที่แม่นยำ:
The heating area and temperature can be precisely controlled using specific induction heating equipment to ensure the accuracy and consistency of metal melting. This precise control can reduce energy waste and material loss and improve production efficiency.
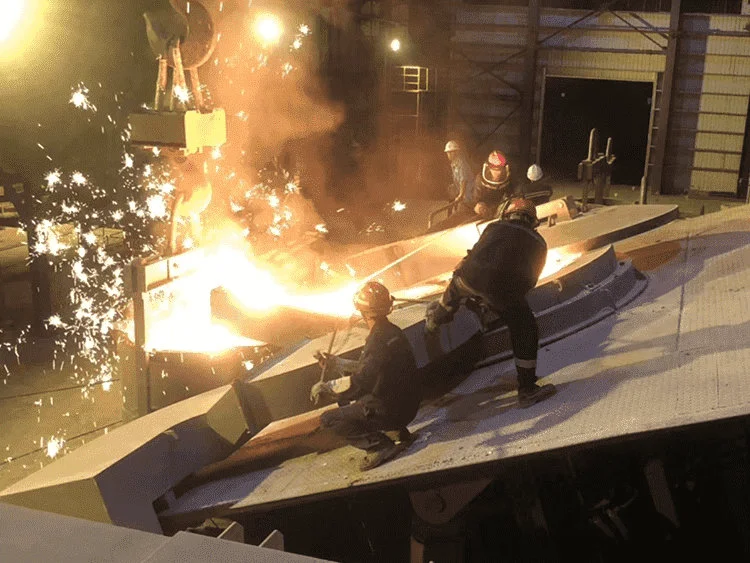
Advantages of induction melting process
1. ให้ความร้อนอย่างรวดเร็ว:
The metal can be quickly heated to the required temperature, ประหยัดเวลาและพลังงาน.
2. การควบคุมที่แม่นยำ:
The heating process can be precisely controlled to avoid overheating or overcooling, ensuring the quality and accuracy of metal materials.
3. Wide applicability:
Can be applied to various metal materials and shapes, improving processing flexibility.
4. Environmentally friendly and efficient
เมื่อเทียบกับวิธีการทำความร้อนแบบดั้งเดิม, induction heating reduces energy waste and has no waste gas emissions, ดังนั้นจึงเป็นมิตรกับสิ่งแวดล้อมมากขึ้น.
Applications of induction melting
การหล่อโลหะ: Induction melting is a common application in metal casting. Through induction heating, metal can be melted quickly and is suitable for casting parts of various shapes and sizes. This technology is commonly used in casting processes in automobile manufacturing, การบินและอวกาศ, machinery manufacturing and other fields.
Metal Alloy Preparation: Induction melting is also widely used to prepare metal alloys. By controlling the melting temperatures and proportions of different metallic materials, alloys with specific properties and compositions can be precisely prepared for various applications such as aerospace, electronic equipment, ฯลฯ.
Metal Recycling: This technology also plays an important role in metal recycling. Through induction melting, scrap metal can be efficiently melted and reused to make new metal products, helping to reduce resource waste and environmental burden.
Precision Casting: Induction melting is particularly useful in castings that require high precision and complex shapes. It can precisely control melting temperature and metal flow to produce high-quality, higher-precision parts, which are commonly used in high-end machinery, medical equipment and other fields.
Special alloy research and development: Research and development of special alloys is also one of the important applications of induction melting. Researchers can use this technology to explore new metal alloy combinations and properties, bringing innovation to the fields of materials science and engineering.
Electronic equipment manufacturing: In the field of electronic equipment manufacturing, induction melting also has important applications. ตัวอย่างเช่น, it is used to produce metal conductors and components in electronic components, ensuring their high purity and precision.
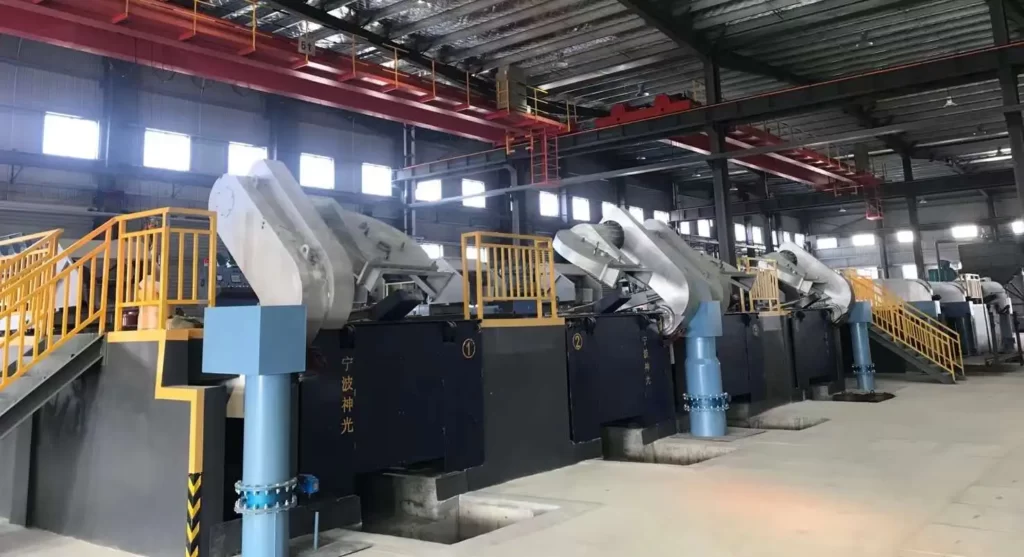
Types of induction melting equipment
Medium Frequency Induction Furnace:
Medium frequency induction furnace is one of the most common and commonly used types. It operates in the mid-frequency range (โดยทั่วไปแล้วระหว่าง 1 kHz and 10 khz) and is suitable for many metal processing areas such as casting, smelting and heat treatment. This type of induction furnace provides medium-frequency induction heating with high efficiency and applicability.
High Frequency Induction Furnace:
High frequency induction furnaces operate in a higher frequency range (usually above 10 khz). This type of induction furnace heats faster and is more suitable for surface heating and fine processing. It is commonly used in areas such as welding, ดับ, coating and special alloy preparation.
Ultra-high frequency induction furnace (Radio Frequency Induction Furnace):
UHF induction furnaces operate in a higher frequency range (usually above 100 khz). This type of induction furnace has faster heating speed and higher heating efficiency, and is suitable for applications that require highly precise heating and strict heating time requirements, such as electronic equipment manufacturing and other fields.
Electron Beam Induction Furnace:
This type of induction furnace uses an electron beam as the heating source. By controlling the energy and focus of the electron beam, highly precise heating can be achieved and used in high-precision processing fields such as the preparation of special metal alloys and precision casting.
Linear induction heating systems (Induction Heating Systems):
Such devices include different forms and structures and can be customized according to needs. They may be suitable for large or specially shaped workpieces and can offer a variety of heating modes and control options to meet a variety of machining needs.