Induction furnaces are a kind of thermal processing equipment. Its basic principle is to use electromagnetic induction to convert electrical energy into thermal energy, and heat metal or other conductive materials through the electromagnetic field generated by the induction coil.
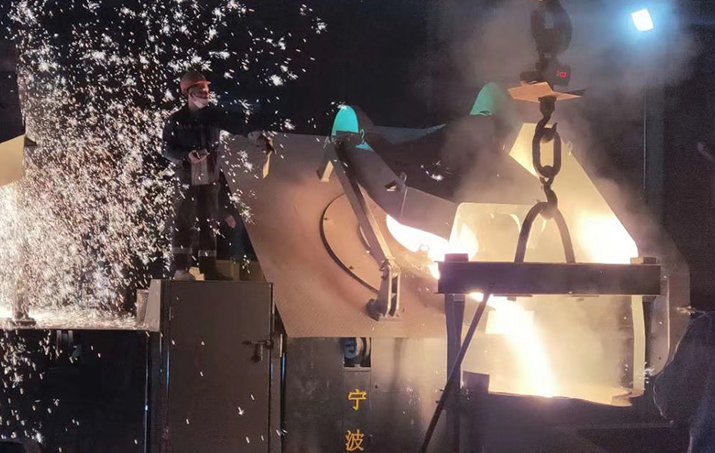
Induction Frequency
Frequency is a key parameter in the working principle of induction furnaces, which determines the effect and applicability of electromagnetic induction heating. Induction furnaces with different frequencies are suitable for different applications, and the choice of frequency has an important impact on the control and performance of the heating process.
The following are the main functions of induction furnace frequency:
Heating depth and uniformity: The frequency determines the penetration depth of the electromagnetic field. High-frequency induction furnaces have a shallow penetration depth and are suitable for heating surfaces or shallow areas, so they can achieve rapid heating and higher surface temperatures. Low-frequency induction furnaces have greater penetration depth and can be used to heat thicker materials, but generally heat more slowly.
Temperature Control: High-frequency induction furnaces are very effective for achieving rapid heating and precise temperature control because they can generate high temperatures quickly. Medium and low-frequency induction furnaces are more advantageous in applications requiring greater temperature uniformity because they can better maintain temperature uniformity.
Material type: Induction furnaces with different frequencies have different suitability for different types of materials. High-frequency and ultra-high-frequency induction furnaces are suitable for metals and materials with good electrical conductivity, such as copper and aluminum. Low-frequency induction furnaces can be used to heat materials with lower electrical conductivity, such as some non-metallic materials.
Power requirements: High-frequency induction furnaces typically require higher power to maintain high-frequency operation, which can result in higher energy consumption. Low-frequency induction furnaces generally require less power but may result in more wasted energy in some cases due to longer heating times.
Application fields: Induction furnaces with different frequencies are suitable for different application fields. For example, high-frequency induction furnaces are commonly used in fine processing fields such as quenching, coating, heat treatment, and electronic manufacturing. Low-frequency induction furnaces are more suitable for heating and metal smelting of large workpieces.
Induction furnaces are mainly divided into low-frequency induction furnaces, medium-frequency induction furnaces, high-frequency induction furnaces, ultra-high-frequency induction furnaces, and power-frequency induction furnaces according to frequency range. Each type has unique applications and advantages in different fields.

Low-frequency induction furnace
Low-frequency induction furnaces typically operate in a lower frequency range, usually below 1000 Hz. This type of induction furnace finds widespread use in applications such as soil improvement, metal heating, and ore smelting. Due to their lower frequency, low-frequency induction furnaces require larger coils and equipment and are primarily used in specific applications.
Medium frequency induction furnace
The frequency range of medium-frequency induction furnaces is usually between 1 kilohertz (kHz) and 10 kilohertz (kHz). This type of induction furnace is very common in metal heat treatment, forging, and other industrial applications. Medium-frequency induction furnaces offer high efficiency and precise temperature control, making them excellent in applications requiring high-temperature uniformity and rapid heating.
High-frequency induction furnace
The operating frequency of high-frequency induction furnaces is usually between 10 kilohertz (kHz) and 100 kilohertz (kHz). It plays an important role in metal quenching, surface coating, and other fine processing fields. High-frequency induction furnaces provide fast and even heating for a variety of fine machining applications.
UHF induction furnace
UHF induction furnaces have a higher frequency range, usually between 100 kilohertz (kHz) and 2 megahertz (MHz). This type of induction furnace is widely used in areas such as electronic component manufacturing and heating of small parts. Due to its high frequency, UHF induction furnaces are able to provide very precise heating and are suitable for applications requiring a high degree of control and precision.
Power frequency induction furnace
Power frequency induction furnaces typically operate in a lower frequency range, typically below 1 kilohertz (Hz). It plays a key role in metal smelting, the heating of large workpieces, and the power industry. Power frequency induction furnaces have lower frequencies and require larger coils and equipment, but are very important in certain applications.
Different types of induction furnaces each have specific advantages and areas of application. Selecting the appropriate induction furnace type depends on the desired heating process, workpiece size, and temperature control requirements. As technology continues to evolve, various types of induction furnaces will continue to play a key role in industrial and non-industrial applications, increasing efficiency and reducing energy consumption while providing high-quality heating and processing solutions. Induction furnaces have become an indispensable tool for modern industrial heating and processing, bringing many important advantages to the production process.