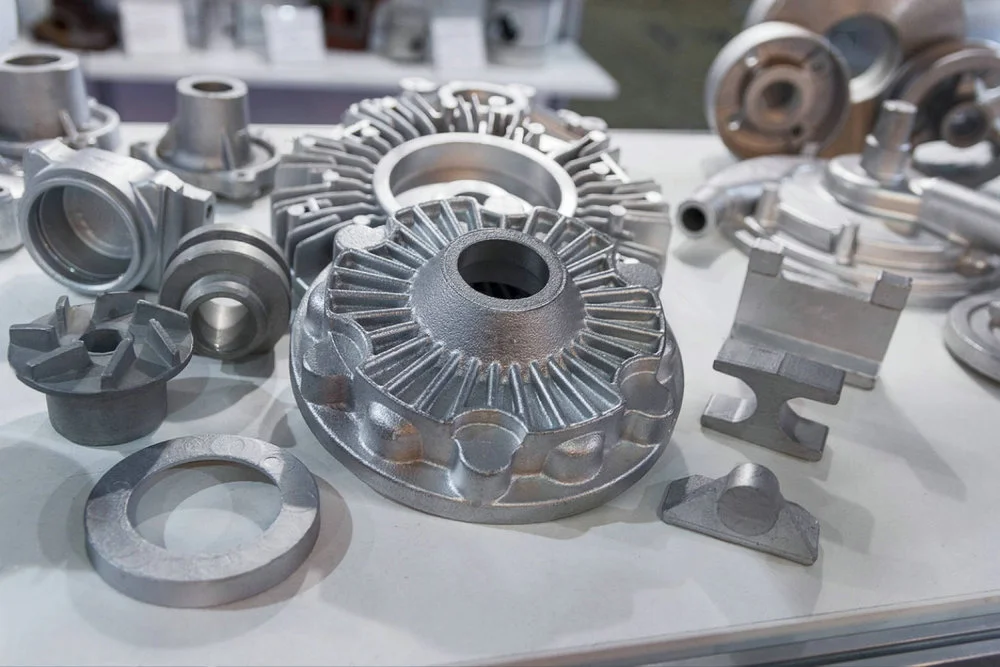
Pori-pori subkutan pada coran adalah cacat yang umum, requiring a series of preventive and corrective measures. Below are specific methods and suggestions for addressing this issue.
I. Preventive Measures
1. Control of Raw Materials
- Avoid raw materials with high titanium (Ti), aluminium (Al), and high-alloy steel content, including stainless steel.
- Thoroughly clean raw materials with severe rust, oxidation, minyak, or waste sand before use.
- Dry wet materials before use to prevent gas absorption.
- Control the size of raw materials to about 300-400mm. When loading the furnace, arrange them tightly to minimize space and reduce oxidation and gas absorption in molten iron.
2. Optimizing the Smelting Process
- Clean slag thoroughly 2-3 times during the melting process, and cover molten iron with slag and insulation materials after cleaning to prevent oxidation.
- The high-temperature holding time for molten iron should not exceed 10-15 minutes to avoid quality deterioration.
- Keep tapping temperatures above 1540±10°C, removing slag promptly and covering with slag insulation to prevent cooling and oxidation.
- Avoid using carbon enhancers that don’t meet standards.
3. Control of Pouring Process
- Thoroughly dry all pouring tools, especially large and small ladles. Never use wet tools or rely on molten iron to heat-dry the equipment.
- Increase the pouring temperature and adopt a fast, high-temperature pouring method, following the “slow-fast-slow” principle. Increasing the temperature by 30-50°C can significantly reduce pore formation.
- Ensure proper slag blocking and shielding, and remove oxide scale before pouring.
4. Sand Treatment
- Keep sand moisture content below 3.5%. Maintain sand permeability at 130-180, wet compressive strength at 120-140 KPa, compaction rate at 35-38%, and surface hardness over 90.
- Use high-quality bentonite and coal powder, and add new sand according to regulations.
- After sand mixing, reclaim excess molding sand and thoroughly clean the sand mixer.
5. Mold Design
- Incorporate exhaust grooves, ducts, and dark air chambers in the parting surfaces to reduce gas pressure in the mold.
- Additional dark air chambers can further minimize gas pressure.
6. Use of Additives
- Menambahkan 4%-6% coal powder, 2% hematite powder, atau 2%-2.5% ammonium difluoride to sand molds to prevent subcutaneous pores.
- Bake the inoculant to remove moisture before use. The inoculant particle size should be 5-10mm, and the aluminum content below 1%.
II. Repair Measures
If subcutaneous pores have already appeared, the following repair methods can be employed:
1. Welding Repair
- Suitable for repairing cast iron or cast steel by filling the pores through welding.
2. Brazing Repair
- Best for low-melting-point metals such as aluminum alloys.
3. Reheat Treatment
- Reheat the casting to recrystallize the pores, followed by machining to repair the surface.
4. Filling Repair
- Use high-strength metal fillers to fill the pores, then recast or machine the casting.
5. Grinding Repair
- Grind the surface to expose the pores, then weld or braze to repair the casting.
III. Inspection and Monitoring
- Regularly inspect castings using visual, ultrasonic, X-ray, or magnetic particle methods to detect subcutaneous pores early.
- Continuously monitor raw materials, peleburan, pouring processes, sand treatment, and mold design to prevent pore formation.

Kesimpulan: Addressing subcutaneous pores in castings requires a holistic approach, including controlling raw materials, optimizing the smelting process, managing pouring techniques, and improving mold design. By implementing comprehensive measures, this defect can be effectively minimized or prevented.