
Paduan berbasis nikel yang meleleh dalam tungku frekuensi menengah menuntut perhatian yang cermat untuk mencegah masalah umum seperti pori-pori, Inklusi Terak, dan oksidasi. Sifat unik dari paduan berbasis nikel, termasuk kepadatan tinggi dan fluiditas yang buruk, mengharuskan langkah-langkah spesifik untuk memastikan pencairan berkualitas tinggi.
1. Memanfaatkan tubuh tungku yang baru dipanggang
Untuk mengurangi pembentukan inklusi terak, Dianjurkan untuk menggunakan badan tungku yang baru dipanggang selama produksi paduan berbasis nikel. Lapisan tungku segar membantu mempertahankan integritas komposisi paduan, Mengurangi kemungkinan pembentukan terak dalam pencairan.
2. Menggunakan agen komposit kalsium-aluminium
Sebelum memulai proses peleburan, Pastikan kemurnian paduan meleleh dengan memperkenalkan agen komposit kalsium-aluminium. Agen ini memfasilitasi penciptaan terak bawah, berkontribusi pada kebersihan keseluruhan dari meleleh dan meminimalkan masalah terkait slag.
3. Menggunakan penutup gas inert
Untuk menangkal penyerapan udara oleh logam cair suhu tinggi selama proses pencairan, menggunakan penutup gas lembam di atas permukaan paduan cair. Praktik ini secara efektif mencegah oksidasi dan meminimalkan kehilangan elemen logam karena pembakaran. Selain itu, Ini meningkatkan kualitas metalurgi dari paduan dan meningkatkan hasil casting.
Dengan mematuhi praktik terbaik ini, Produsen dapat mengoptimalkan proses pencairan paduan berbasis nikel di tungku frekuensi menengah, memastikan kualitas dan konsistensi yang unggul dalam produk akhir mereka.
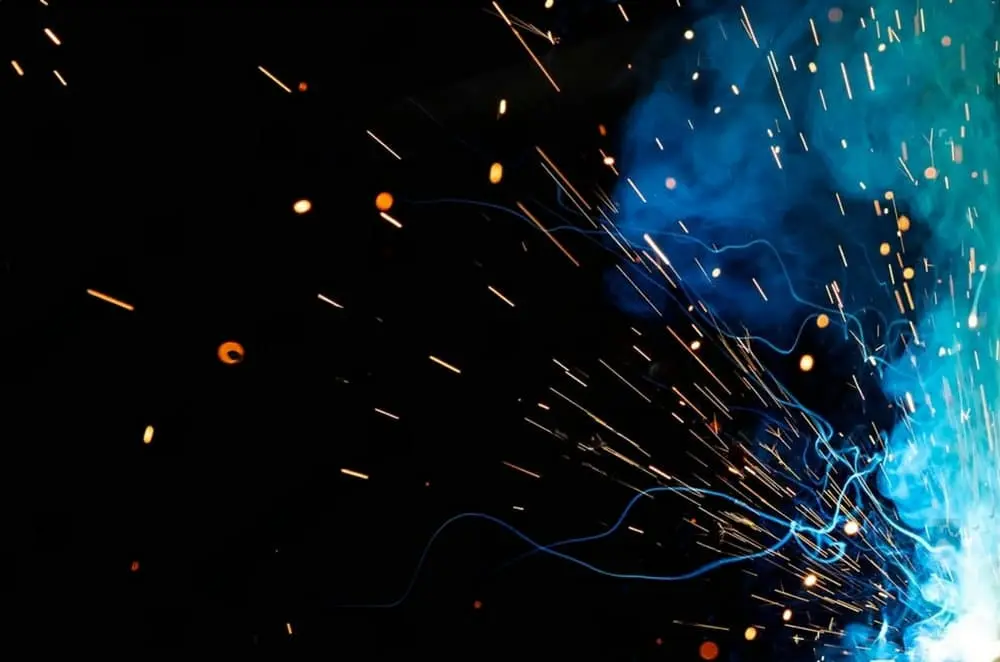