The most efficient metal melting furnace can depend on several factors, including the type of metal being melted, the scale of the operation, energy sources, and environmental considerations. Generally, the following types of furnaces are considered efficient for different purposes:
1. Induction Furnaces
- Kahusayan: Induction furnaces are highly efficient, with thermal efficiency often exceeding 90%. They use electromagnetic induction to heat and melt metals.
- Advantages: Fast melting times, precise temperature control, reduced oxidation, and energy efficiency.
- Applications: Ideal for steel, iron, aluminyo, copper, and other non-ferrous metals.
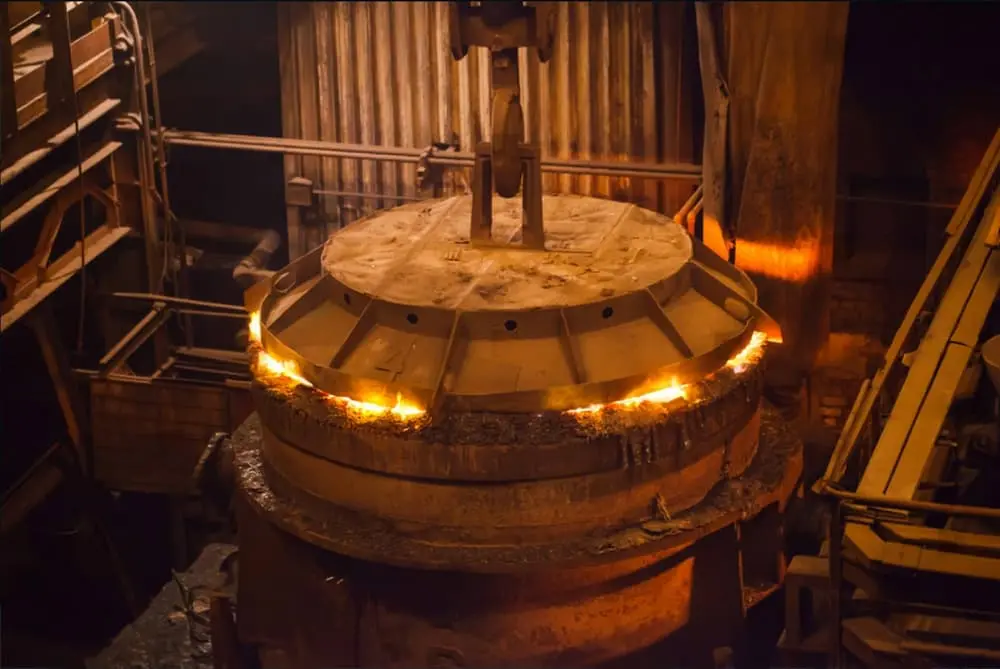
2. Electric Arc Furnaces (EAF)
- Kahusayan: EAFs are very efficient, particularly for steel production. They convert electrical energy into heat to melt scrap steel and direct reduced iron (DRI).
- Advantages: Flexibility in the types of scrap materials used, high productivity, and reduced CO2 emissions compared to traditional blast furnaces.
- Applications: Predominantly used in steelmaking, particularly in mini-mills.
3. Crucible Furnaces
- Kahusayan: Depending on the heat source (electric, gas, or coke), crucible furnaces can be relatively efficient for small-scale operations.
- Advantages: Simple construction, versatility, and suitability for melting small batches of various metals.
- Applications: Often used for melting non-ferrous metals like aluminum, brass, and bronze.
4. Rotary Furnaces
- Kahusayan: Rotary furnaces can be quite efficient for recycling aluminum and other non-ferrous metals.
- Advantages: Effective for processing large quantities of scrap material, good mixing, and uniform heating.
- Applications: Common in aluminum recycling and other non-ferrous metal industries.
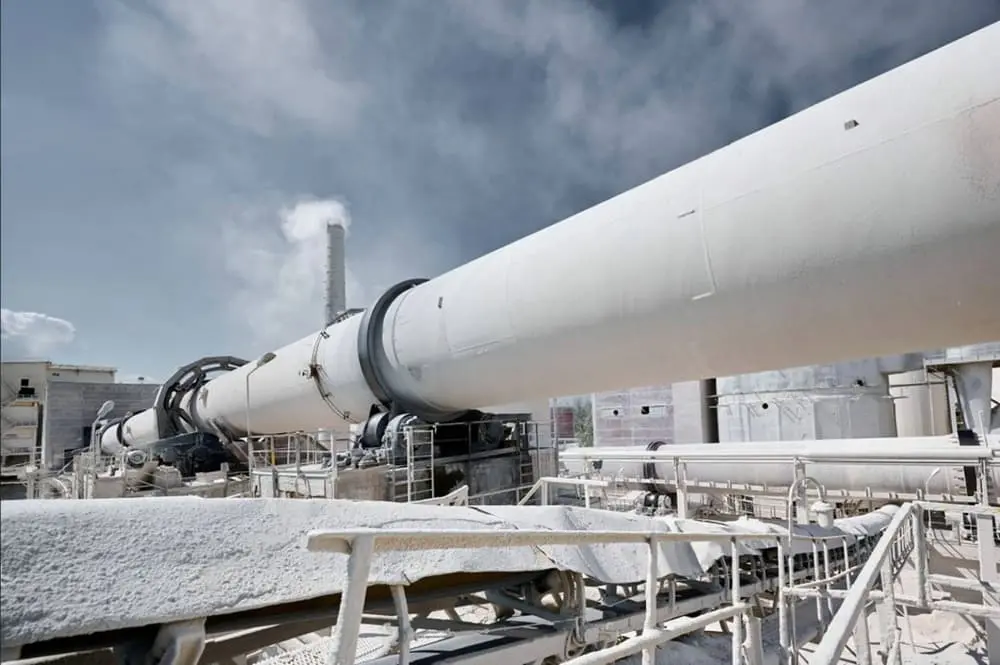
5. Reverberatory Furnaces
- Kahusayan: Modern reverberatory furnaces can be quite efficient, particularly when equipped with regenerative burners and heat recovery systems.
- Advantages: Large capacity, ability to handle a wide range of scrap materials, and good fuel efficiency.
- Applications: Used in aluminum, copper, and other non-ferrous metal industries.
Factors Influencing Efficiency
- Insulation: Proper insulation reduces heat loss and improves thermal efficiency.
- Pinagmulan ng Enerhiya: Electric furnaces are typically more efficient and environmentally friendly than fossil-fuel-based furnaces.
- Automation and Control Systems: Advanced control systems can optimize the melting process, reducing energy consumption and improving efficiency.
- Maintenance: Regular maintenance ensures the furnace operates at peak efficiency.
For the highest efficiency in a specific application, it is essential to consider the type of metal being melted, production scale, energy costs, and environmental impact. Induction furnaces and electric arc furnaces are generally considered among the most efficient options in modern metalworking.