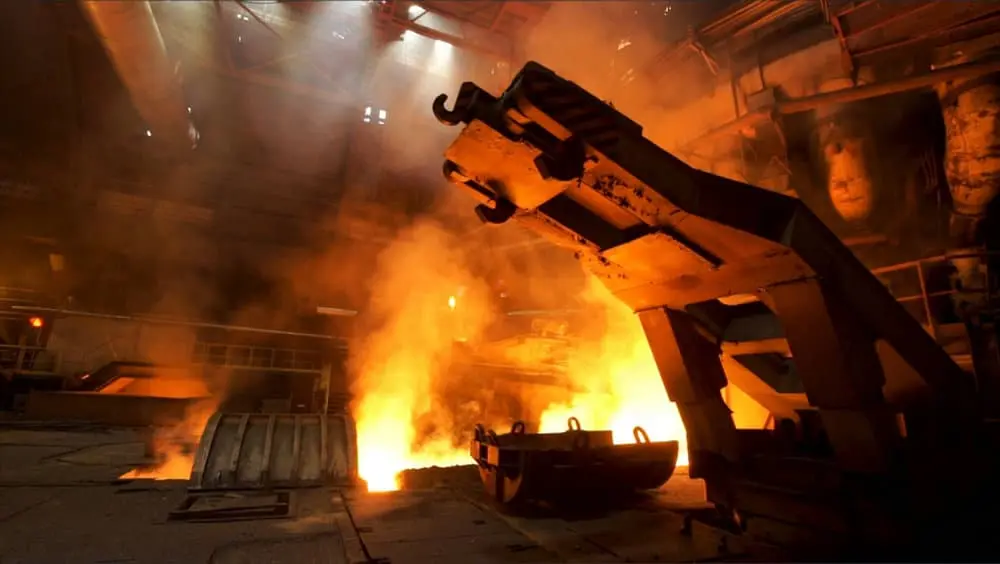
Ang smelting furnace ay isang dalubhasang pugon na ginagamit para sa pagtunaw ng iba't ibang mga ores, pangunahin ang mga bakal na bakal, to produce steel and non-ferrous metals. Below are some common types of smelting furnaces and their specific functions.
Blast Furnace
Application: Widely used for the rough smelting of metals such as copper, lead, lead-zinc, and antimony.
Structure: Comprises a furnace top, furnace body, main bed (or throat), furnace cylinder, and tuyere device.
Function: Solid materials including smelting charge (concentrate, sintered ore), coke, flux, and counter-materials are added from the top. High-pressure air is blown into the tuyere, initiating melting, oxidation, reduction, and chemical reactions as materials move upward. Liquid metal, matte, and slag are discharged from the furnace bottom, while gases and metal oxides are expelled through the top outlet.
Kaldo Furnace
Alias: Oxygen oblique blown converter.
Features: The tilting and rotating furnace body enhance contact between liquid metal and slag, improving reaction efficiency.
Refractory Damage Factors: Similar to the Isa furnace (Ausmelt furnace).
Oxygen Bottom Blowing Lead Smelting Furnace
Structure: A horizontal cylindrical reactor designed for efficient lead smelting.
Volatilization Kiln
Application: A rotary kiln used for treating leached slag and recovering valuable metals like Zn, Pb, In, and Ge.
Features: The temperature in the intermittent reaction zone can reach 1300–1500℃.
Flash Furnace
Application: The primary equipment for flash smelting in non-ferrous metal processes.
Features: High production efficiency and low energy consumption, with high SO₂ concentration in flue gas.
Structure: Composed of a reaction tower, sedimentation tank, vertical flue, and nozzle.
Function: Dried powdered concentrate is mixed with hot air or oxygen in the nozzle and injected at high speed (60–70 m/s) into the reaction tower, where the smelting processes occur rapidly (within 2–3 seconds). The resulting molten sulfide and oxide drop into the sedimentation tank for further processing.
Electric Furnace
Application: Used for smelting, heating, and heat treatment of steel, ferroalloys, and non-ferrous metals.
Classification: Includes resistance furnaces, induction furnaces, arc furnaces, plasma furnaces, and electron beam furnaces.
Function: Electric furnaces are essential for drying, roasting, refining, natutunaw na, insulation, and slag treatment in non-ferrous metal smelting.
- Induction pugon: Utilizes the induction heating effect, ideal for heating and melting steel, copper, aluminyo, and zinc. It features fast heating and low material loss, making it suitable for automatic production lines.
- Arc Furnace: Employs arc thermal effects for melting; it can be categorized into indirect, direct, and submerged arc furnaces.
- Vacuum Arc Furnace: Specialized for melting reactive and refractory metals such as titanium, molybdenum, and niobium.
- Plasma Furnace: Uses ionized working gas to generate plasma for heating or melting materials.
In summary, various types of smelting furnaces are employed in metal smelting, each designed with specific structures, principles, and applications. Selecting the appropriate smelting furnace requires careful consideration of the metal type, production scale, energy consumption, and environmental impact.