Sa modernong produksyong industriyal, pagkukubli, bilang isang mahalagang metal processing technique, is widely used in automotive, aerospace, machinery, at iba pang mga larangan.
The pre-forging heating process is a key factor affecting the quality of forgings and production efficiency.
Traditional heating methods often suffer from high energy consumption, low efficiency, and significant pollution, making it difficult to meet the development needs of the modern forging industry.
The emergence of induction furnaces has brought a revolutionary change to the forging industry.
Advantages of Induction Furnaces in the Forging Industry
- High Efficiency and Energy Saving
- Induction heating technology enables fast and uniform heating, greatly shortening heating time and improving production efficiency.
- Compared to traditional coal-fired heating, induction furnaces have higher thermal efficiency and lower energy consumption, effectively reducing production costs.
- Reduced preheating time and lower standby energy consumption further enhance energy utilization.
- Precise Temperature Control
- Medium frequency furnaces can precisely control heating temperatures, ensuring that billets are forged within the optimal temperature range, improving the uniformity of the forging’s structure and its mechanical properties.
- Precise temperature control reduces defects such as overheating and cracking, improving the yield of forgings.
- Heating parameters can be flexibly adjusted for different materials and forging processes, enabling personalized customization.
- Environmental Friendliness and Cleanliness
- Induction furnaces use electrical energy for heating, producing no smoke or waste gas emissions, which meets the environmental requirements of modern industry.
- Reduced environmental pollution, improved working conditions, and protection of worker health.
- Complies with national energy conservation and emission reduction policies, contributing to sustainable enterprise development.
- Simple Operation and Intelligence
- Medium frequency furnaces have a high degree of automation and are easy to operate, reducing the labor intensity of workers.
- Modern medium-frequency furnaces are equipped with intelligent control systems that enable remote monitoring and fault diagnosis, improving equipment reliability and maintenance efficiency.
- Automated heating can be achieved through parameter presets, reducing the requirement for worker skill levels.
- Improved Forging Quality
- Due to the uniform heating, internal stress generated during forging can be reduced, and the mechanical properties of forgings can be improved.
- Reduce the generation of oxide scale, make the surface quality of forgings better.
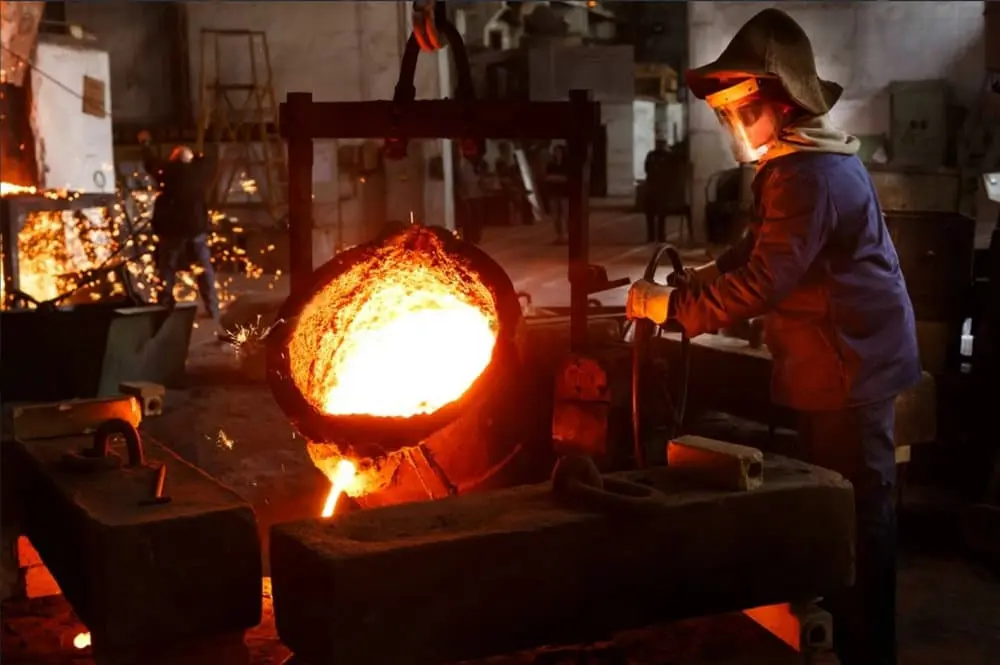
Applications of Induction Furnaces in the Forging Industry
- Pre-Forging Heating
- Induction furnaces can quickly and uniformly heat various metal billets, providing high-quality billets for forging.
- Widely used in the forging of automotive parts (such as crankshafts, connecting rods, gears), hardware tools (such as wrenches, hammers, pliers), standard parts (such as bolts, nuts), and other products.
- Inductors can be flexibly adjusted for different billet specifications to achieve efficient heating.
- Induction Through Heating
- Induction through heating technology can achieve uniform overall heating of billets, improving the mechanical properties of forgings.
- Suitable for the forging of long shaft parts (such as drive shafts, rolls), bar stock parts (such as bars, mga tubo), and other products.
- In the production of large forgings, medium frequency induction through heating technology can significantly improve production efficiency and forging quality.
- Local Heating
- Induction furnaces can achieve localized heating of workpieces, which is used in some special forging processes, such as heating the surface of gears and bearings to perform localized heat treatment and improve the wear resistance of workpieces.
- Post-Forging Heat Treatment
- After forging, parts can be heat treated by induction furnaces, such as quenching and tempering.
Looking to the Future
With the continuous advancement of technology, the technology of medium frequency furnaces is also constantly developing. Intelligentization, automation, and energy conservation will be the future development trends of medium frequency furnaces. We believe that medium frequency furnaces will play an increasingly important role in the forging industry, injecting strong momentum into the high-quality development of the forging industry.
Konklusyon
With their advantages of high efficiency and energy saving, precise temperature control, and environmental cleanliness, medium frequency furnaces have become an indispensable and important piece of equipment in the modern forging industry. Choosing high-quality medium frequency furnaces will bring higher efficiency and better benefits to your forging production.