Induction furnaces are a cornerstone of the modern foundry industry, offering a clean, efficient, and controllable method for melting various metals. Their application spans a wide range of processes and materials.
1. Melting a Wide Range of Metals:
- Induction furnaces can efficiently melt ferrous metals like iron and steel (including all grades). This is a major application, with many iron foundries replacing older cupola furnaces due to the environmental and efficiency advantages.
- They are also highly effective for melting non-ferrous metals such as:
- Aluminum and its alloys: Offering energy-efficient melting with minimal oxidation.
- Copper and copper alloys (brass, bronze): Providing precise temperature control and low metal loss.
- Sink: Used in galvanizing and cathode melting processes.
- Precious metals (gold, pilak na pilak, platinum group metals): Allowing for refining and use in jewelry manufacturing.
- Induction furnaces can also handle more specialized metals like silicon (for semiconductors and solar-grade silicon), reactive metals, rare earth metals, titan, and more.
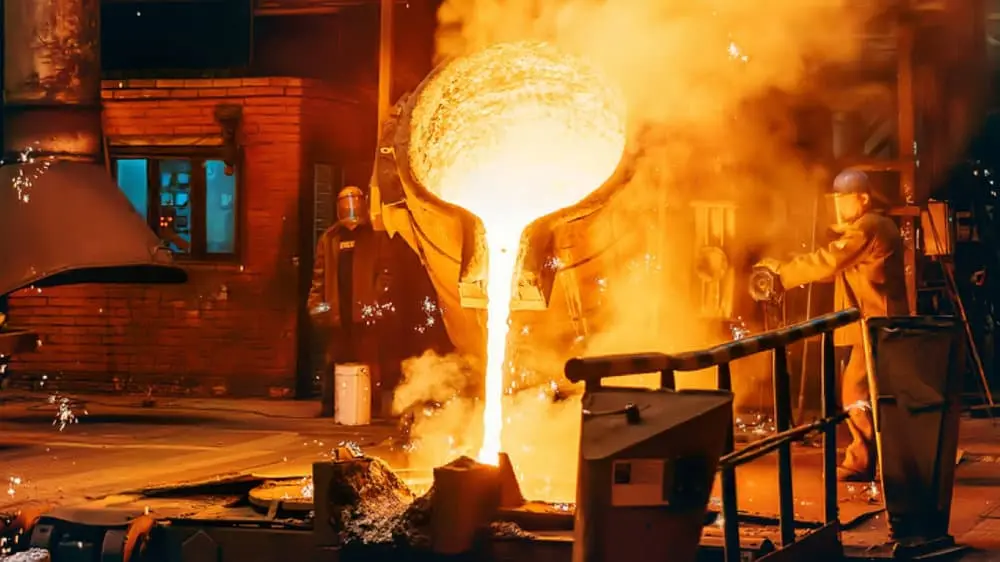
2. Alloying:
Induction furnaces are ideal for alloy manufacturing due to the excellent stirring action created by the electromagnetic field. This ensures a homogeneous mixture and uniform chemical composition throughout the melt.
The precise temperature control minimizes the loss of valuable alloying elements through oxidation.
3. Investment Casting:
Induction melting is widely used in investment casting for melting various metals, including superalloys and precious metals, often in air or vacuum furnaces.
4. Die Casting:
Induction furnaces can provide a consistent supply of molten metal at the desired temperature for die casting processes, particularly for non-ferrous metals like aluminum and zinc.
5. Holding and Superheating:
Channel-type induction furnaces are often used for holding molten metal at a specific temperature before pouring, ensuring consistent quality.
They can also be used to superheat metal that has been initially melted in another furnace.
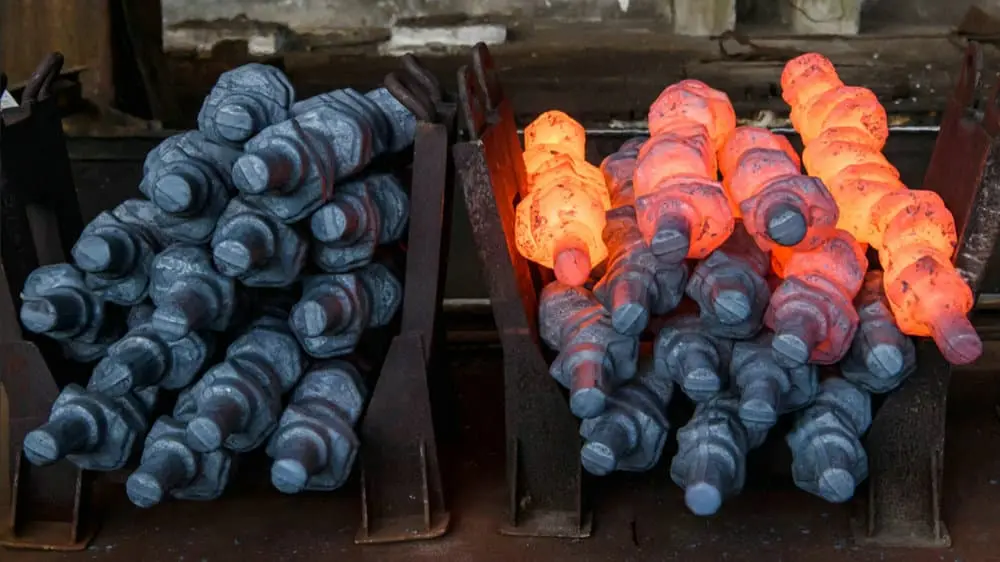
6. Other Applications:
- Pre-forging heating: Induction heating is used to bring metal billets to the required temperature for forging.
- Lunas sa init: Applications include steel bar quenching and tempering.
- Melting for continuous casting: Channel furnaces are particularly suited for high-throughput operations with continuous casting schedules.
Types of Induction Furnaces Used in Foundries:
There are two main types of induction furnaces used in foundries:
- Coreless Induction Furnace: This type is widely used for melting various ferrous and non-ferrous alloys. The metal is placed in a crucible surrounded by a water-cooled copper coil. The alternating current in the coil induces eddy currents in the metal, causing it to heat and melt. Coreless furnaces offer flexibility for alloy changes and can be started cold.
- Channel Induction Furnace: This type has a loop or channel containing molten metal that acts as a secondary winding in a transformer. The primary coil induces a current in the molten metal loop, causing heating. Channel furnaces are often used for melting low melting point alloys and as holding furnaces for higher melting point alloys. They are well-suited for continuous operation with fewer alloy changes.
Mga hurno ng induction are a versatile and crucial technology in the foundry industry, enabling efficient and high-quality production of a wide range of metal castings. Their advantages in terms of energy efficiency, environmental impact, and metallurgical control have made them a preferred choice for many modern foundries.