আনয়ন চুল্লি বিভিন্ন ধরনের আসে, প্রাথমিকভাবে তাদের নকশা উপর ভিত্তি করে শ্রেণীবদ্ধ, ফাংশন, and application.
1. কোরলেস ইন্ডাকশন ফার্নেস
- Description: The coreless induction furnace is the most common type used in the metal casting industry. It uses an electromagnetic field to induce currents in the metal, which generates heat and melts it.
- অ্যাপ্লিকেশন: Typically used for melting ferrous and non-ferrous metals like steel, cast iron, অ্যালুমিনিয়াম, তামা, and brass.
- Advantages:
- High energy efficiency.
- সুনির্দিষ্ট তাপমাত্রা নিয়ন্ত্রণ.
- Ability to melt a variety of metals.
- Common Uses: Foundries, steel plants, and metal processing industries.
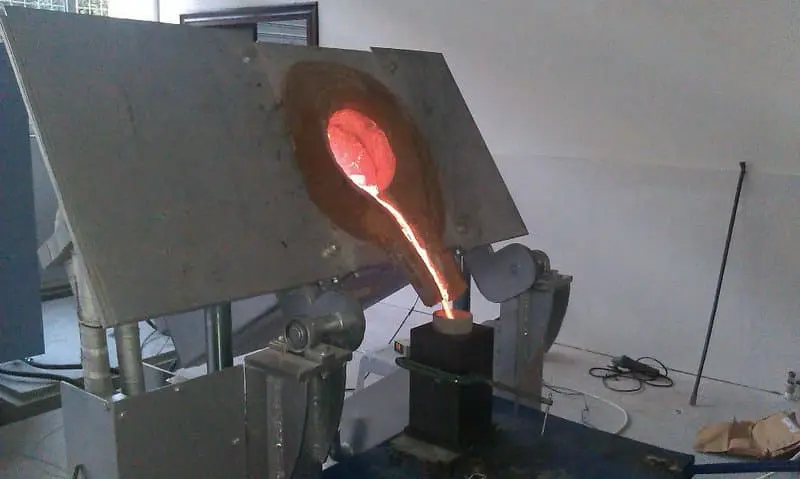
2. Channel Induction Furnace
- Description: This type uses a series of channels or a channel-shaped coil to create a magnetic field. The metal is melted within the channel, and the design is typically more compact than the coreless version.
- অ্যাপ্লিকেশন: Mainly used for melting lower quantities of metal or for specific alloys like aluminum and brass.
- Advantages:
- Compact and efficient.
- Lower capital cost than coreless furnaces.
- Common Uses: Small to medium-sized foundries, scrap metal recycling.
3. Induction Melting Furnace with a Crucible
- Description: এই নকশায়, a crucible is placed within the induction coil, and the metal inside the crucible is melted by the electromagnetic field.
- অ্যাপ্লিকেশন: Often used for high-temperature melting applications such as precious metals (সোনা, প্লাটিনাম) or specialized alloys.
- Advantages:
- Good for small batches of metal.
- Highly efficient in energy transfer.
- Common Uses: Jewelry casting, small batch processing.
4. Vacuum Induction Furnace (VIF)
- Description: A vacuum induction furnace operates under reduced pressure, which helps minimize oxidation and contamination of the molten metal. The furnace works similarly to coreless or channel furnaces but in a vacuum environment.
- অ্যাপ্লিকেশন: Used for high-purity metals and alloys, such as titanium, aerospace-grade materials, and special steels.
- Advantages:
- Produces high-quality, low-contamination metals.
- Ideal for sensitive or reactive materials.
- Common Uses: মহাকাশ, automotive, and high-performance alloys.
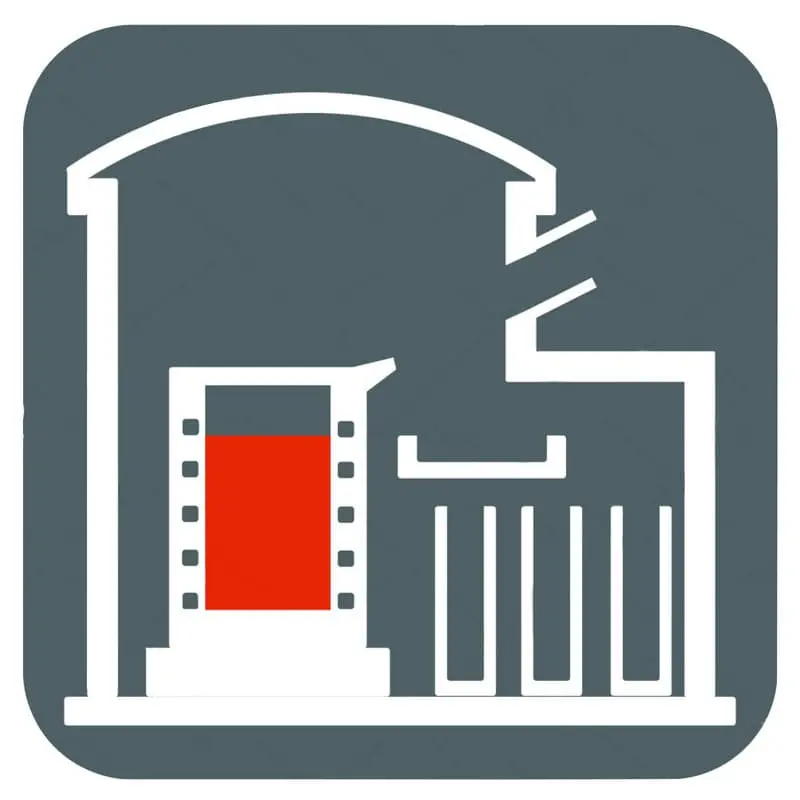
5. Induction Furnace with a Metal Foam Core
- Description: This is an innovative variation where a foam-like metal structure is created within the furnace. It helps improve heat distribution and efficiency during the melting process.
- অ্যাপ্লিকেশন: Used for producing high-efficiency alloys, improving metal quality, and reducing energy consumption.
- Advantages:
- Better energy efficiency.
- Uniform temperature distribution.
- Common Uses: Aluminum alloy production, lightweight metals.
6. Rotary Induction Furnace
- Description: This type involves a rotating drum or tilting mechanism that allows the furnace to move metal during the melting process, enhancing mixing and even heat distribution.
- অ্যাপ্লিকেশন: Primarily used for applications where uniform alloying and high-speed metal melting are needed.
- Advantages:
- Efficient heat transfer.
- Homogeneous metal melting.
- Common Uses: Scrap metal recycling, alloy processing.
Each type of induction furnace is chosen based on factors like metal type, required melting capacity, energy efficiency, and specific industry needs.