ইন্ডাকশন ফার্নেসে দস্তা গলানো একটি প্রক্রিয়া যা বিভিন্ন শিল্পে গ্যালভানাইজিংয়ের জন্য ব্যবহৃত হয়, ডাই-কাস্টিং, এবং মিশ্র উত্পাদন. ইন্ডাকশন চুল্লিগুলিতে দস্তা গলে যাওয়ার বিষয়ে আপনার কিছু মূল পয়েন্ট এখানে রয়েছে:
1. ইন্ডাকশন হিটিং নীতি
ইন্ডাকশন চুল্লিগুলি তাপ উত্পন্ন করতে বৈদ্যুতিন চৌম্বকীয় আনয়ন ব্যবহার করে. একটি বিকল্প বর্তমান একটি কয়েল দিয়ে যায়, একটি চৌম্বকীয় ক্ষেত্র তৈরি করা যা ধাতুতে এডি স্রোতকে প্ররোচিত করে, তাপ উত্পাদন এবং দস্তা গলে.
2. গলিত দস্তা তাপমাত্রা নিয়ন্ত্রণ
জিংক প্রায় 419.5 ডিগ্রি সেন্টিগ্রেডের তুলনামূলকভাবে কম তাপমাত্রায় গলে যায় (787.1°ফা). ইন্ডাকশন চুল্লিগুলি সুনির্দিষ্ট তাপমাত্রা নিয়ন্ত্রণের প্রস্তাব দেয়, যা জিংকের অতিরিক্ত গরম এবং জারণ প্রতিরোধের জন্য গুরুত্বপূর্ণ.
3. দক্ষতা এবং গতি
আনয়ন চুল্লিগুলি অত্যন্ত দক্ষ, জিংকের দ্রুত গরম এবং গলে যাওয়া সরবরাহ করা. এই দক্ষতা শক্তি খরচ এবং অপারেশনাল ব্যয় হ্রাস করে.
4. পরিবেশগত প্রভাব
ইন্ডাকশন চুল্লিগুলি traditional তিহ্যবাহী জীবাশ্ম-জ্বালানী-চালিত চুল্লিগুলির তুলনায় কম নির্গমন উত্পাদন করে, তাদের আরও পরিবেশগতভাবে বন্ধুত্বপূর্ণ করে তোলা. তারা কম স্ল্যাগ উত্পাদন করে, বর্জ্য হ্রাস.
5. গলে গুণমান
ইন্ডাকশন গলে যাওয়া একটি অভিন্ন এবং ধারাবাহিক গলিত সরবরাহ করে, যা উচ্চমানের দস্তা পণ্যগুলির জন্য প্রয়োজনীয়. প্রক্রিয়াটি দূষণকে হ্রাস করে এবং খাদটির রচনার উপর আরও ভাল নিয়ন্ত্রণের অনুমতি দেয়.
6. সুরক্ষা বিবেচনা
ইনহেল করা হলে দস্তা ধোঁয়াগুলি বিপজ্জনক হতে পারে, সুতরাং সঠিক বায়ুচলাচল এবং ফিউম এক্সট্রাকশন সিস্টেমগুলি প্রয়োজনীয়. অতিরিক্তভাবে, অপারেটরদের ব্যক্তিগত প্রতিরক্ষামূলক সরঞ্জাম ব্যবহার করা উচিত (পিপিই) গলিত ধাতব স্প্ল্যাশ এবং ধোঁয়াগুলির এক্সপোজার এড়াতে.
7. আনয়ন চুল্লি প্রকার
- কোরলেস আনয়ন চুল্লি: জিংকের ছোট থেকে মাঝারি আকারের ব্যাচ গলে যাওয়ার জন্য উপযুক্ত. তারা নমনীয়তা এবং দ্রুত টার্নআরাউন্ড সময় দেয়.
- চ্যানেল আনয়ন চুল্লি: অবিচ্ছিন্ন গলে যাওয়া এবং প্রচুর পরিমাণে দস্তা ধরে রাখার জন্য আরও ভাল. এগুলি প্রায়শই উচ্চ উত্পাদন হারের সাথে ফাউন্ড্রিগুলিতে ব্যবহৃত হয়.
8. ক্রুসিবল নির্বাচন
ক্রুশিবল উপাদানের পছন্দ গুরুত্বপূর্ণ. গ্রাফাইট এবং সিরামিক ক্রুশিবলগুলি সাধারণত তাপীয় শক এবং রাসায়নিক ক্ষয়ের উচ্চ প্রতিরোধের কারণে দস্তা গলানোর জন্য ব্যবহৃত হয়.
9. পাওয়ার সাপ্লাই
ইন্ডাকশন চুল্লিগুলির জন্য একটি বিদ্যুৎ সরবরাহের প্রয়োজন যা দস্তা গলানোর জন্য নির্দিষ্ট পাওয়ার প্রয়োজনীয়তাগুলি পরিচালনা করতে পারে. বিদ্যুৎ সরবরাহ অবশ্যই চুল্লি ক্ষমতা এবং গলানোর হারের সাথে মেলে অবশ্যই.
10. রক্ষণাবেক্ষণ এবং ডাউনটাইম
দক্ষ অপারেশন নিশ্চিত করার জন্য আনয়ন চুল্লিগুলির নিয়মিত রক্ষণাবেক্ষণ প্রয়োজনীয়. এর মধ্যে কয়েল পরীক্ষা করা অন্তর্ভুক্ত রয়েছে, বিদ্যুৎ সরবরাহ, কুলিং সিস্টেম, এবং পরিধান এবং ক্ষতির জন্য ক্রুশিবল.
11. ব্যয় বিবেচনা
যদিও ইন্ডাকশন চুল্লিগুলি traditional তিহ্যবাহী চুল্লিগুলির তুলনায় উচ্চতর ব্যয় রয়েছে, তাদের অপারেশনাল দক্ষতা, কম শক্তি খরচ, এবং পরিবেশগত প্রভাব হ্রাস দীর্ঘমেয়াদী ব্যয় সাশ্রয় হতে পারে.
12. অ্যাপ্লিকেশন
- গ্যালভানাইজিং: জারা প্রতিরোধের জন্য লেপ ইস্পাত এবং লোহার জন্য দস্তা গলানো.
- ডাই-কাস্টিং: স্বয়ংচালিত জন্য দস্তা ডাই-কাস্ট অংশ উত্পাদন, ইলেকট্রনিক্স, এবং অন্যান্য শিল্প.
- খাদ উত্পাদন: বিভিন্ন শিল্প অ্যাপ্লিকেশনগুলির জন্য দস্তা ভিত্তিক অ্যালো তৈরি করা.
এই দিকগুলি বোঝার জন্য আপনাকে জিংক গলানোর জন্য আনয়ন চুল্লিগুলি কার্যকরভাবে ব্যবহার করতে সহায়তা করবে, সুরক্ষা নিশ্চিত করা, দক্ষতা, এবং উচ্চ মানের উত্পাদন.
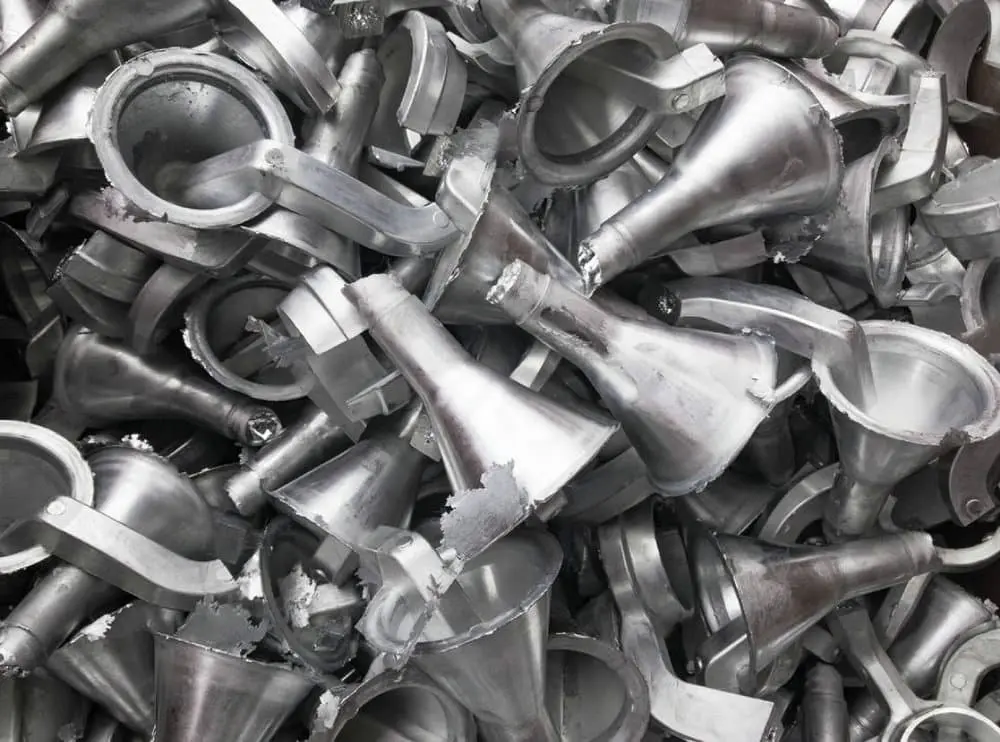