The role of furnace lining in induction metal melting furnace
The furnace lining in an induction metal melting furnace plays a critical role in ensuring efficient and safe operation, as well as prolonging the lifespan of the furnace equipment.
The choice of lining material depends on factors such as the operating temperature, the type of metal being melted, and the specific requirements of the application.
- Thermal insulation: The lining helps to contain the heat generated by the induction coils within the furnace, preventing excessive heat loss to the surroundings. This insulation ensures efficient heating of the metal charge and helps maintain the desired temperature throughout the melting process.
- Protection against heat and chemical corrosion: The lining material must be able to withstand the high temperatures generated by the induction coils and resist chemical reactions with the molten metal and any fluxes or additives used in the melting process. This protection extends the lifespan of the furnace and reduces maintenance requirements.
- Electrical insulation: The lining material should have good electrical insulation properties to prevent short circuits between the induction coils and the metal charge. This insulation helps maintain the efficiency and safety of the induction heating process.
- Structural support: The lining provides structural support for the furnace walls, ensuring that they maintain their shape and integrity under the thermal and mechanical stresses experienced during operation.
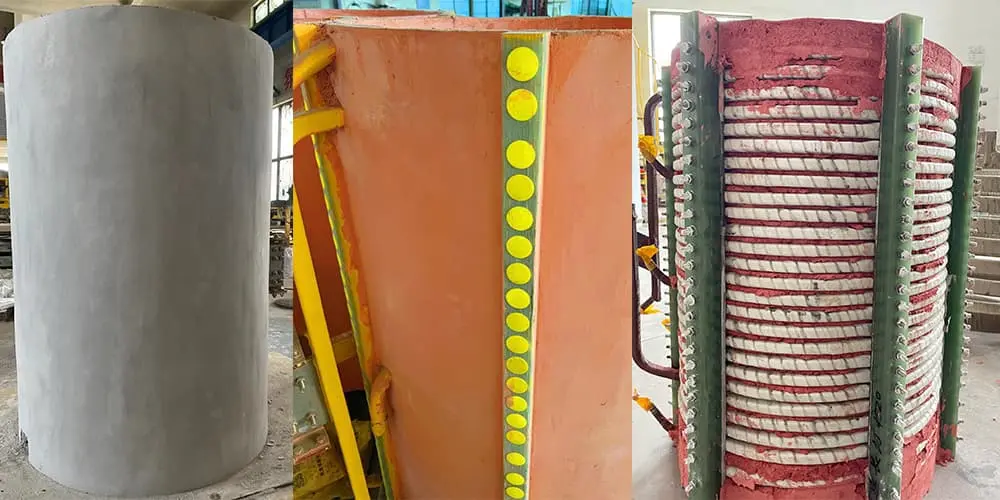
Common material is used for furnace lining
Furnace linings are typically made of materials that can withstand high temperatures and resist chemical reactions with the substances being processed within the furnace. Some common materials used for furnace lining include:
- Refractory bricks: These are made of ceramic materials that can withstand high temperatures. They are often used in the construction of furnace walls and floors.
- Refractory castables: These are mixtures of refractory aggregates, binders, and additives that can be poured or cast into place to form furnace linings. They offer flexibility in shape and are often used in complex furnace geometries.
- Ceramic fibers: These are lightweight and highly insulating materials made from alumina, السيليكا, or other refractory materials. They are used as insulation layers within furnace linings to reduce heat loss.
- Refractory coatings: These are thin layers of refractory materials that are applied to the surface of furnace linings to provide additional protection against heat and chemical corrosion.
- Refractory mortars: These are special types of mortar used to bond refractory bricks or castables together in furnace construction.
The choice of material depends on factors such as the operating temperature of the furnace, the type of materials being processed, and the specific requirements of the application.
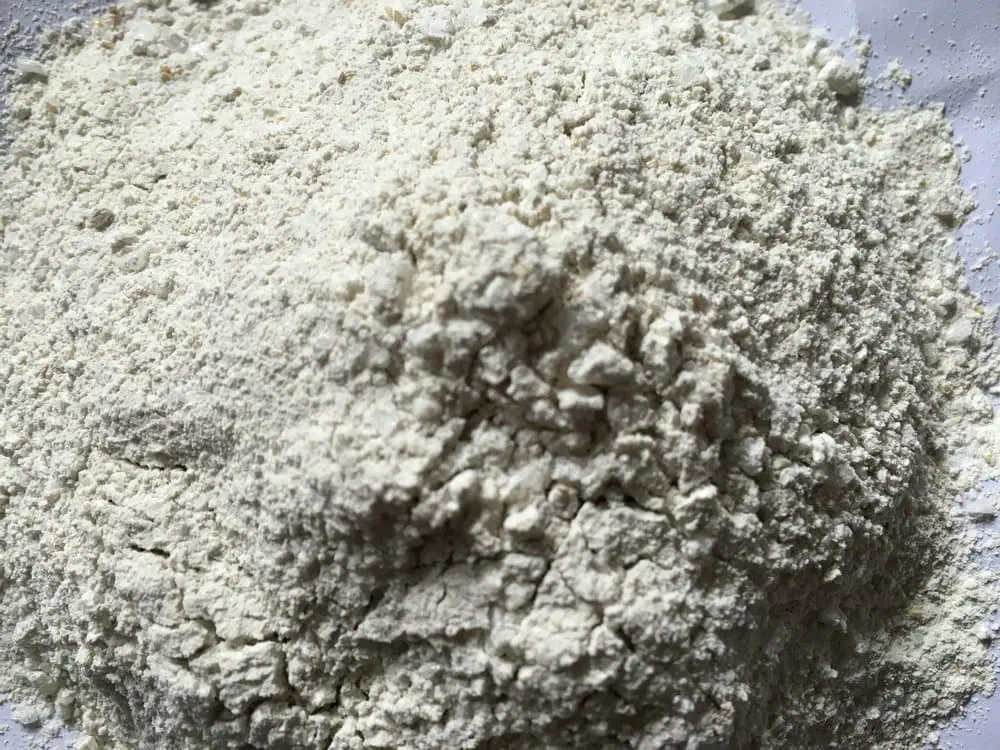
Refractory lining design and optimization
Refractory lining design and optimization is a critical aspect of furnace engineering, aiming to maximize the performance, longevity, and efficiency of the lining while minimizing costs and downtime.
Material selection: Choose refractory materials based on factors such as operating temperature, chemical composition of the processed materials, الموصلية الحرارية, mechanical strength, and resistance to thermal shock and chemical corrosion. Consider using different types of refractories (على سبيل المثال, fire clay, high alumina, السيليكا, magnesia) in combination to achieve optimal performance.
Thickness optimization: Determine the appropriate thickness of the refractory lining based on factors such as heat transfer requirements, thermal expansion properties of the materials, and expected wear and erosion rates. Thicker linings provide better insulation and protection but may increase costs and reduce furnace capacity.
Thermal expansion control: Prevent cracking and spalling of the refractory lining due to thermal expansion and contraction by designing expansion joints, incorporating flexible joints or expansion loops, and selecting refractory materials with compatible thermal expansion coefficients. Proper expansion joint design is essential to accommodate thermal stresses without compromising the integrity of the lining.
Joint design and installation: Ensure proper alignment, tightness, and sealing of joints between refractory bricks or castable sections to minimize heat loss, gas leakage, and infiltration of molten metal or slag. Use refractory mortars, gaskets, or sealing compounds to fill gaps and create a continuous barrier against thermal and chemical attacks.
Thermal insulation: Incorporate insulation materials (على سبيل المثال, ceramic fibers, vermiculite, perlite) into the refractory lining design to reduce heat loss, تحسين كفاءة الطاقة, and maintain uniform temperature distribution within the furnace. Optimize insulation thickness and placement to minimize thermal gradients and heat transfer losses.
Computational modeling and simulation: Use advanced modeling techniques (على سبيل المثال, finite element analysis, computational fluid dynamics) to simulate heat transfer, stress distribution, and thermal cycling behavior in refractory linings. These simulations help optimize design parameters, identify potential failure modes, and predict the performance of alternative lining configurations.
Monitoring and maintenance: Implement regular inspection, monitoring, and maintenance protocols to detect signs of wear, erosion, thermal degradation, or chemical attack in the refractory lining. Schedule periodic repairs, refurbishments, or relining to extend the service life of the furnace and ensure safe and efficient operation.
By applying these principles and practices, engineers can design and optimize refractory linings that meet the specific requirements of different furnace applications, ranging from high-temperature metallurgical processes to thermal treatment and incineration systems. Effective refractory lining design and optimization contribute to enhanced furnace performance, reduced downtime, and improved overall productivity and profitability.
