في مجال معالجة المعادن, يستخدم الألمنيوم على نطاق واسع بسبب الموصلية الكهربائية الممتازة, الموصلية الحرارية, واللدونة. يعتبر ذوبان الألمنيوم خطوة حاسمة في سلسلة معالجة الألومنيوم, واختيار الفرن المناسب أمر ضروري لضمان كفاءة الانصهار, جودة المنتج, وحماية البيئة. تستكشف هذه المقالة أنواع الأفران المستخدمة عادة لذوبان الألومنيوم وخصائصها لمساعدة القراء على اتخاذ قرارات مستنيرة.
1. الفرن الكهربائي
الأفران الكهربائية هي من بين أكثر المعدات شيوعًا لذوبان الألومنيوم, تقديم التحكم الدقيق في درجة الحرارة وعملية ذوبان نظيفة. يتم تصنيفها بشكل أساسي إلى نوعين: أفران الحث وأفران المقاومة.
فرن الحث: يستخدم هذا الفرن الحث الكهرومغناطيسي لتوليد التيارات الدوامة داخل آبوب الألمنيوم, تمكين التدفئة السريعة والموحدة. أفران الحث ذات كفاءة عالية, توفير التحكم الدقيق في درجة الحرارة واستخدام الطاقة العالية, جعلها الخيار المفضل لشركات معالجة الألمنيوم الكبيرة.
فرن المقاومة: في هذا النوع, يتم تسخين الألومنيوم بواسطة التيار يمر عبر عناصر المقاومة. على الرغم من أن سرعة التدفئة أبطأ نسبيًا, تتميز أفران المقاومة ببنية بسيطة, سهولة الصيانة, وانخفاض التكاليف, جعلها مناسبة لعمليات ذوبان الألمنيوم الصغيرة إلى المتوسطة الحجم.
2. فرن الغاز
تستخدم أفران الغاز غازات قابلة للاحتراق مثل الغاز الطبيعي والبروبان لإذابة الألومنيوم من خلال درجات حرارة عالية الناتج عن الاحتراق. أنها توفر التدفئة السريعة والكفاءة الحرارية العالية, جعلها مثالية للحالات التي تتطلب طاقة حرارية كبيرة, خاصة عندما يكون مصدر الطاقة محدودًا. لكن, تنتج أفران الغاز انبعاثات أعلى ويجب أن تكون مزودة بأنظمة تهوية شاملة وأجهزة معالجة غاز العادم لتلبية متطلبات حماية البيئة.
3. فرن الزيت
على غرار أفران الغاز, يذوب أفران الزيت الألومنيوم باستخدام درجات الحرارة العالية المتولدة من احتراق الوقود, عادة استخدام الوقود السائل مثل الديزل. في حين أن أفران النفط لا تزال لديها تطبيقات محددة (على سبيل المثال, في المناطق ذات الكهرباء غير الكافية), إن استخدامهم يتراجع تدريجيًا بسبب اللوائح البيئية الصارمة بشكل متزايد ودفع مصادر الطاقة الأنظف.
4. دليل الاختيار
عند اختيار فرن لذوبان الألومنيوم, النظر في العوامل التالية.
- مقياس الإنتاج: تحديد نوع الفرن المناسب وسعةه على أساس الإخراج السنوي وحجم الذوبان اليومي. يجب على مؤسسات معالجة الألومنيوم الكبيرة إعطاء الأولوية, خيارات لتوفير الطاقة مثل الأفران التعريفية.
- إمدادات الطاقة: حدد نوع الفرن الأنسب على أساس توافر الطاقة المحلي والتكاليف. قد تفضل المناطق ذات الكهرباء الموثوقة ومعدلات معقولة الأفران الكهربائية, في حين أن المناطق الغنية بالغاز الطبيعي أو تواجه قيود الكهرباء قد تختار أفران الغاز أو الزيت.
- البيئة متطلبات الحماية: مع زيادة اللوائح البيئية, من الضروري للمؤسسات النظر في الانبعاثات والأداء البيئي. يمكن أن تساعد الأفران المنخفضة الانبعاثات والسهلة في التخفيف من المخاطر البيئية وخفض تكاليف التشغيل.
- فعالية التكلفة: تقييم عوامل مثل الشراء, التشغيل, وتكاليف الصيانة لاختيار أكثر أنواع الفرن فعالية من حيث التكلفة.
في ملخص, يعد اختيار الفرن المناسب لذوبان الألومنيوم أمرًا بالغ الأهمية. من خلال فهم خصائص وتطبيقات مختلف الأفران بشكل دقيق والنظر بعناية في الاحتياجات المحددة لعملياتك, يمكنك ضمان كفاءة, مستقر, وعملية ذوبان صديقة للبيئة.
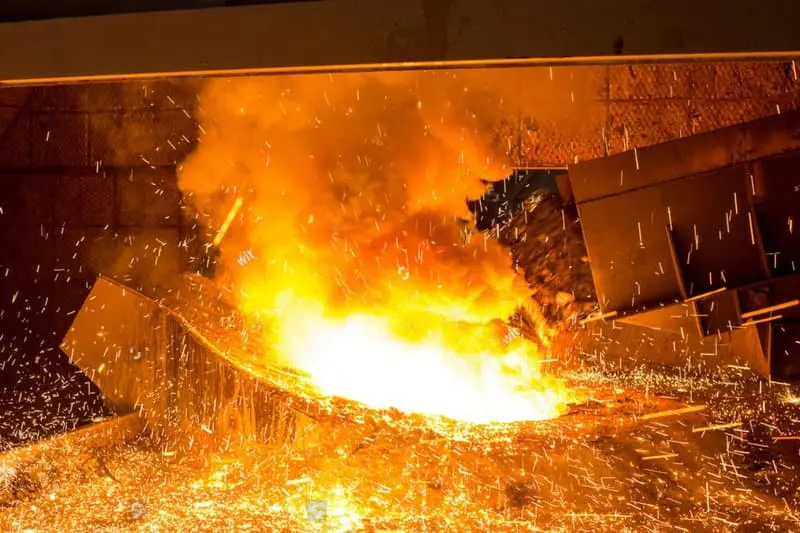