فُولاَذ, معروفة بقوتها, متانة, والتنوع, هو في صميم عدد لا يحصى من الصناعات, ranging from construction to automotive manufacturing. One of the critical steps in steel production is melting the raw materials to create molten steel, which can then be cast, forged, or processed into various products. The melting furnace for steel is essential in this process, offering a reliable and controlled environment to transform solid scrap or alloys into liquid steel. في هذه المدونة, we’ll explore the different types of melting furnaces used for steel, their benefits, and key factors to consider when choosing the right furnace for your operations.
Types of Melting Furnaces for Steel
فرن الصهر التعريفي, Induction melting furnaces are widely used in steel foundries due to their energy efficiency and the ability to melt various steel grades. These furnaces utilize electromagnetic induction to heat and melt the steel, creating a clean and high-quality molten metal. Induction furnaces are known for their rapid melting process, التحكم الدقيق في درجة الحرارة, and reduced risk of contamination, making them ideal for high-precision applications.
Advantages:
- Energy-efficient with minimal heat loss
- Rapid melting and temperature control
- Low maintenance costs
- Suitable for smaller to medium-sized batches
فرن القوس الكهربائي (EAF), The Electric Arc Furnace (EAF) is one of the most commonly used melting furnaces for steel, especially in large-scale steel production. This furnace uses an electric arc to melt the scrap steel, creating temperatures high enough to melt even the toughest alloys. EAFs are commonly used in steel recycling operations, where they convert steel scrap into new steel products.
Advantages:
- Ideal for recycling scrap steel
- High melting capacity for large batches
- Low emissions and improved environmental performance compared to other furnaces
- Capable of producing high-quality steel
فرن الانفجار, While the Blast Furnace is traditionally associated with the production of pig iron, it is also used in the melting of steel in certain processes like the Basic Oxygen Furnace (BOF). The BOF process involves adding oxygen to molten iron to convert it into steel, and a blast furnace can be used to produce the molten iron necessary for this.
Advantages:
- High capacity for large-scale steel production
- Reliable and proven technology for steelmaking
- Works well for bulk production of steel from iron ore
Cupola Furnace, Although not as commonly used for steel, cupola furnaces can melt small quantities of steel and alloys. The cupola is a vertical cylindrical furnace where the steel scrap is melted by coke combustion. The process produces molten metal at a relatively low cost, but it’s generally limited to smaller-scale operations.
Advantages:
- Cost-effective for small-scale operations
- Suitable for producing small quantities of steel
- Lower operational costs compared to more complex furnaces
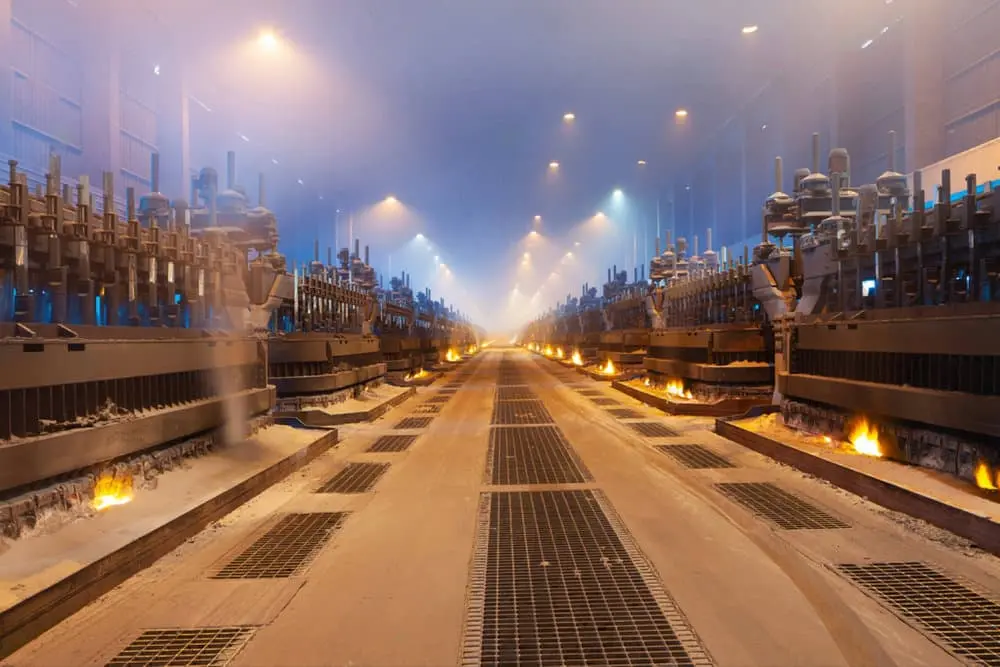
Key Benefits of Melting Furnaces for Steel
- Efficiency and Productivity A well-designed melting furnace optimizes energy consumption while maintaining high throughput. على سبيل المثال, induction furnaces and EAFs offer energy-efficient melting, resulting in lower operational costs and faster turnaround times.
- رقابة جودة Steel quality is heavily influenced by the melting process. Furnaces with advanced control systems allow operators to fine-tune the temperature, composition, and chemistry of the molten steel, ensuring consistent and high-quality results.
- المرونة Different types of furnaces can melt various grades and types of steel, from low-carbon to high-alloy steels. This flexibility allows manufacturers to produce a wide range of steel products and respond to changing market demands.
- التأثير البيئي Modern melting furnaces, particularly EAFs, offer significant environmental benefits. They produce fewer emissions, especially when compared to traditional blast furnaces. This is important for industries striving to reduce their carbon footprint and comply with stricter environmental regulations.
Considerations When Choosing a Melting Furnace for Steel
- Steel Type and Production Volume The type of steel you need to produce and the volume of production will dictate the furnace you choose. High-volume steel production typically requires large furnaces like the Electric Arc Furnace or Blast Furnace, while smaller batches can be melted more efficiently in induction furnaces.
- كفاءة الطاقة Energy costs make up a significant portion of the operational expenses in steel production. Furnaces like induction and EAFs, which offer high energy efficiency, can help reduce these costs in the long run.
- Space and Installation Costs The size and complexity of the furnace will affect the required space and installation costs. Induction furnaces are typically more compact and easier to install, while EAFs and blast furnaces may require more space and significant capital investment.
- صيانة and Downtime Maintaining the furnace to ensure smooth operations is critical for steel manufacturers. Consider the maintenance requirements and potential downtime for repairs or upgrades. أفران الحث, على سبيل المثال, are relatively low-maintenance compared to EAFs or blast furnaces, which may require more frequent attention.
- البيئة Compliance Regulatory requirements related to emissions, waste, and energy consumption are becoming more stringent. Modern melting furnaces are designed to meet environmental standards, so it’s important to choose a furnace that aligns with sustainability goals and complies with local regulations.
خاتمة
The melting furnace for steel is a vital piece of equipment in the steel production process. From the energy-efficient induction furnace to the large-scale electric arc and blast furnaces, there are multiple options for manufacturers to choose from, each offering unique benefits depending on production needs. When selecting the right furnace, it’s essential to consider factors such as production volume, كفاءة الطاقة, steel type, maintenance costs, والتأثير البيئي. By making an informed decision, you can ensure that your steel production process is both cost-effective and sustainable, leading to better quality and higher output.
Whether you’re a small foundry or a large steel mill, understanding the differences between furnace types and how they impact your operations will help you make the right investment for your future.