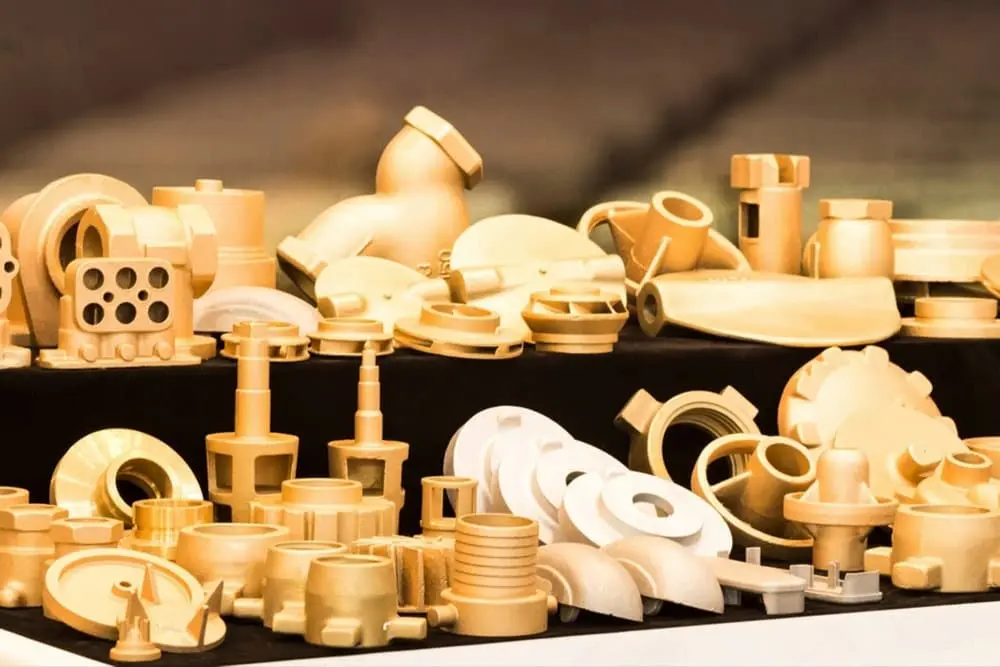
يعد وضع الناهض أمرًا بالغ الأهمية لضمان جودة المسبوكات وسلامتها. Properly positioned risers help feed molten metal into the casting to compensate for shrinkage as it solidifies, preventing defects like porosity and cracks.
Drawing from years of experience in the foundry industry, here are some key guidelines for optimal riser placement:
1. Position Risers Above the Feeding Area
The riser should be placed as high as possible above the part of the casting that needs to be fed. Ideally, it should be positioned next to the last solidified hot node to ensure that the riser can effectively supply molten metal as the casting solidifies. This strategic placement helps to compensate for shrinkage in the thickest sections and minimizes the risk of voids or internal porosity.
2. Avoid Stress Concentration Points
Risers should not be placed at areas where the casting is prone to stress concentrations, such as corners or sharp transitions. Placing risers in these areas can hinder the casting’s natural shrinkage process and may cause cracks. It’s important to consider the casting’s stress distribution when deciding where to place risers.
3. Optimize for Finishing
Another critical factor in riser placement is minimizing finishing time. The riser should be positioned on the surface of the casting that will be cut or machined during the finishing process. This reduces the amount of work required to remove the riser and ensures the casting is as close to the final shape as possible when it comes out of the mold.
4. Use Multiple Risers for Complex Castings
For castings with hot nodes at different heights that require feeding, it may be beneficial to place risers on different horizontal planes. This approach ensures that each hot node is fed effectively during the solidification process. بالإضافة إلى ذلك, chilling iron can be used to separate the feeding range of each riser, improving control over the cooling rate and preventing uneven solidification.
5. Consider Alloy Shrinkage
The type of alloy being cast plays a significant role in determining riser placement. For alloys with large volume shrinkage, such as cast steel, manganese brass, and aluminum bronze, risers should be positioned above or on the side of the thickest part of the casting. These alloys tend to form concentrated shrinkage cavities, and proper riser placement helps prevent these defects by providing adequate feeding.
6. Riser Placement for Alloys with Small Shrinkage
في المقابل, for alloys with small volume shrinkage during solidification, such as gray cast iron, the riser is typically placed opposite the ingate. For these materials, the size of the riser does not need to be overly large, as the shrinkage is less pronounced, and the feeding requirements are lower.
خاتمة
Riser placement is an essential part of the casting process that directly affects the quality of the final product. By considering the casting’s geometry, alloy properties, and the need for efficient finishing, risers can be positioned to optimize metal flow, reduce defects, and enhance overall casting performance. Whether you’re working with complex shapes or simple geometries, understanding the dynamics of riser placement will lead to better results and higher-quality castings.